さて、ようやくきょうの本来の目的地、藤村製糸へ。
藤村製糸は大正6年(1917)に創業した製糸会社で、四国の中ではもちろん、全国的にみても高品質な生糸を生産できる製糸会社として知られていた。国内の蚕糸業が縮小する中で、西日本で最後まで操業した機械製糸工場でもあった。
藤村製糸は私の生まれ故郷群馬県の群馬町と、私が10年間住んだ徳島県の山川町に乾繭工場を持っていた。乾繭工場とは生きた繭を高温で殺蛹し、長距離輸送できるように乾燥させる施設だ。山川町の乾繭工場は以前にお願いして見学させてもらったが、本体の製糸工場は一度も訪れたことがなかった。四国を離れるにあたってどうしても見ておきたいのが藤村製糸本社工場だったのだ。
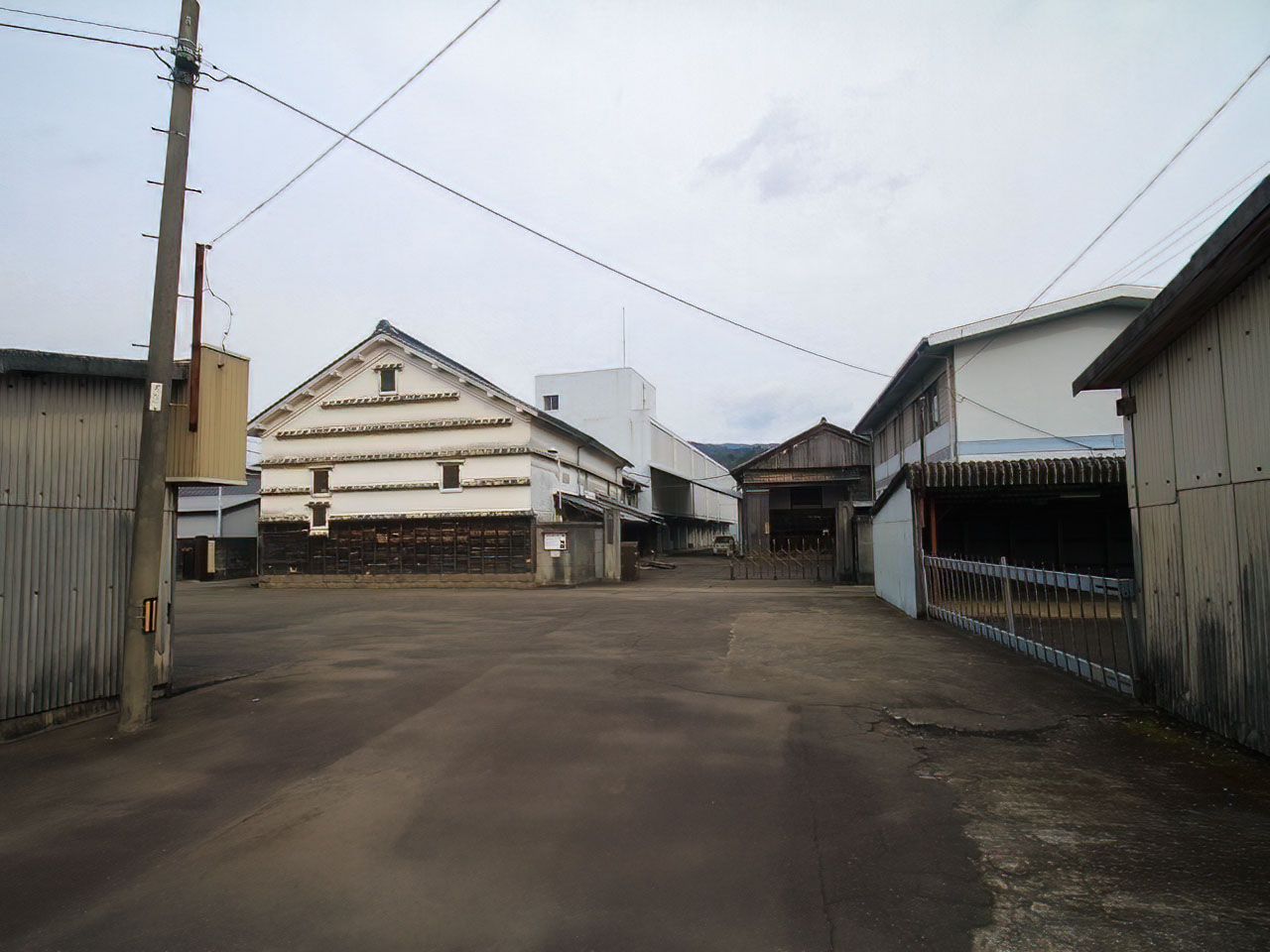
藤村製糸は平成17年(2005)までこの地で操業。その後、経営破綻したカネボウのブラジル工場を引き継いでブラジルで生糸を生産した。そのブラジルの事業も2010年には引き上げ、いまは細々と特殊なシルク製品を製造しているだけで、現在工場は動いていない。
入口には水切り瓦の土蔵造の繭蔵があり、歴史を感じさせる。予約すれば工場内を見学は可能。きょうは13時から見せていただけることになっていた。
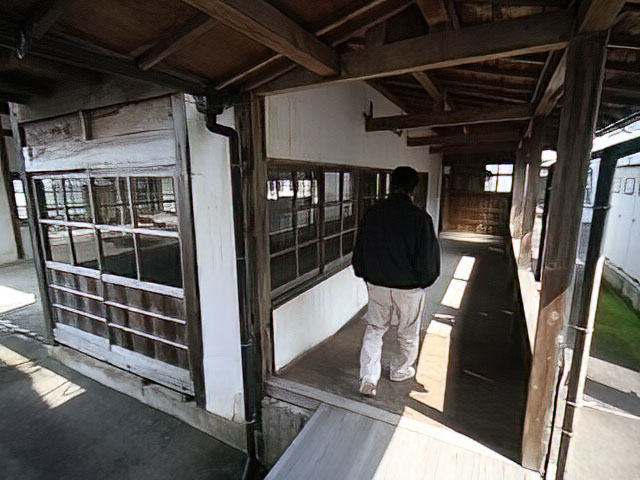
専務さんはに乾繭工場を見せていただいたときに徳島でお会いしていて3年ぶり。覚えていてくださったみたい。
工場は操業しておらず、電灯も点いていないので暗かったが、かなりたくさんの写真を撮らせてもらった。ただし動いていない機械ではよくわからないので、製糸工場の基本的な製造工程は碓氷製糸の記事を見てもらうとして、ここでは藤村製糸でしか見られないポイントを中心に書いていこうと思う。
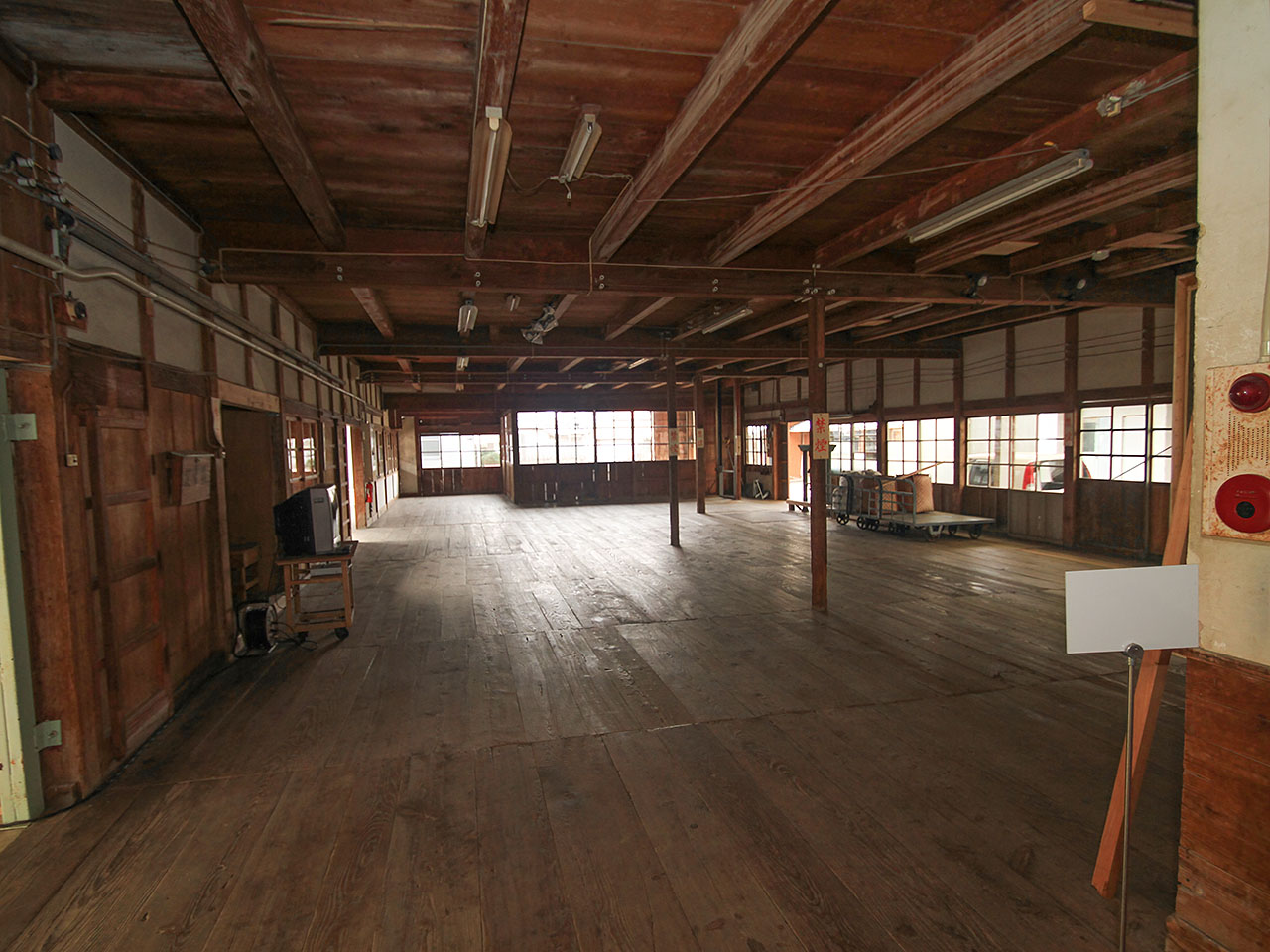
荷受け場。
最後のころ、繭は農協で集荷して工場に運ばれてきていたが、それより古い時代には製糸会社で集荷していた。この場所がその荷受け場だった。この広い部屋一面に繭袋が並んだのだろう。
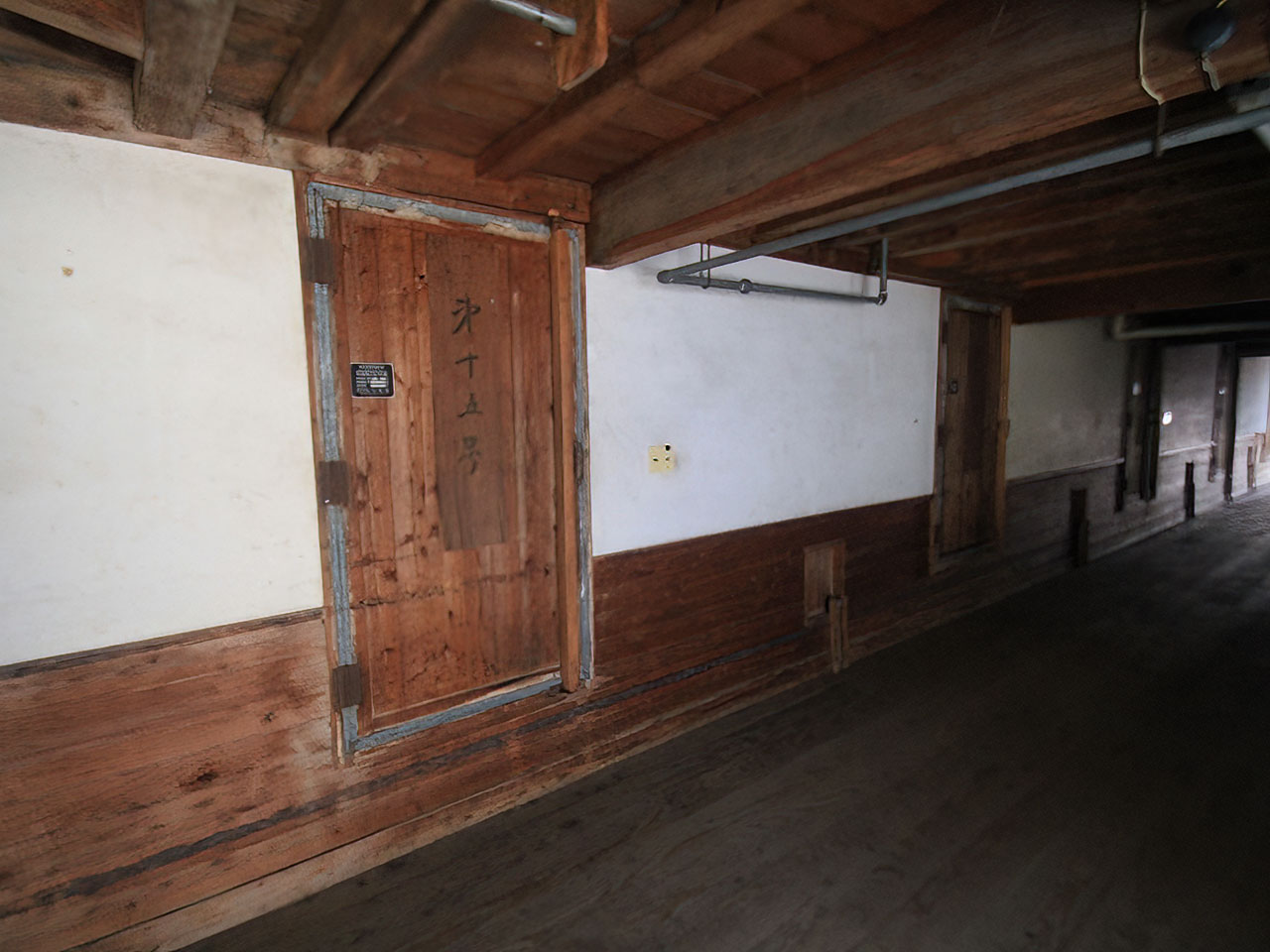
藤村製糸の施設の一番の特徴は、この土蔵式の低温乾燥機だろう。
扉に「㐧十五号」と書いてあるからわかるが、多くの小部屋に分かれている乾繭機なのだ。
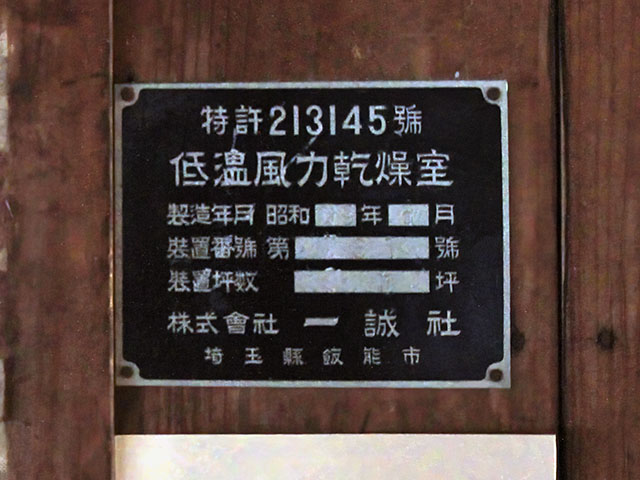
コーションプレートを見るとメーカーは株式会社一誠社とある。埼玉県飯能市の会社だ。現在も会社があるのかはわからない。
飯能というと、入間地方には全国でも屈指の製糸会社、石川組製糸があったので、その製糸工場の設立に関係した設備会社だったのかもしれない。
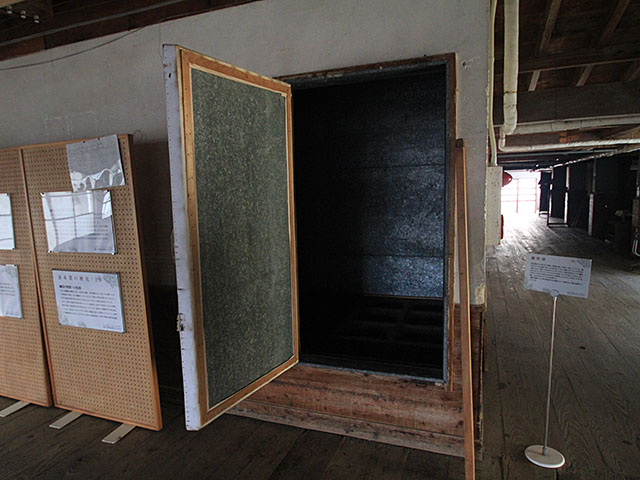
乾繭機の中を見せてもらった。
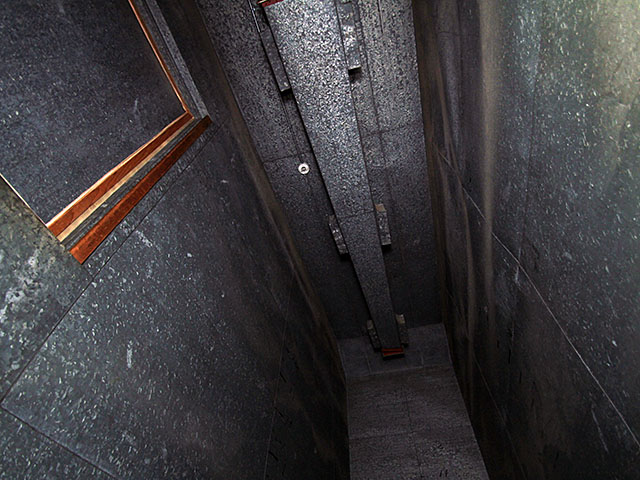
一部屋の乾燥室は奥が意外に長く、かつ天井も高い。
繭を大量に詰め込むので、2階にも投入口がある。
天井にはダクトがありここから温風が吹き込まれる。
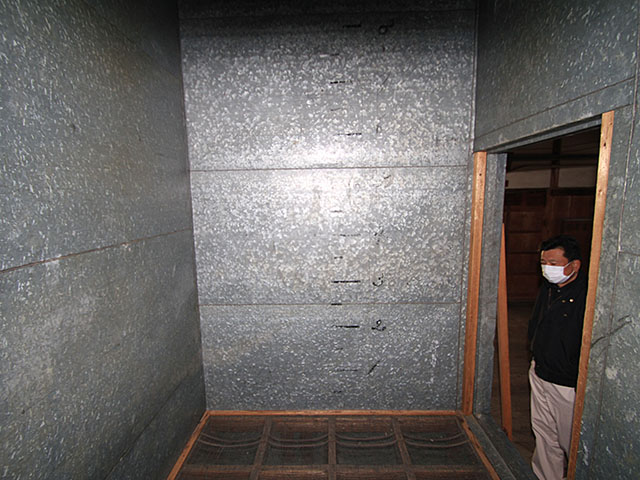
床は金網になっていて、下から温風を抜く仕組みになっている。
繭は繭袋から出してバラ繭として投入される。
一度に投入するのではなく、壁にある目盛りに沿って少しずつ入れては乾燥させるという。
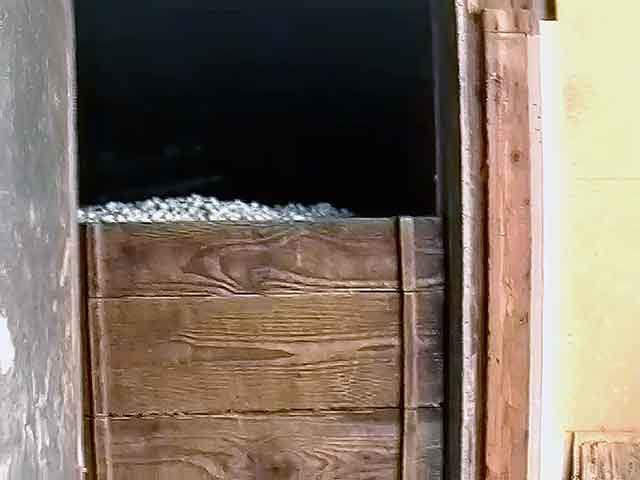
操業していた当時の様子。板倉のように入口に板をはめていく。3時間ごとに30cm入れては平らにして乾燥していくのだという。
(徳島県秋田淳子氏撮影)
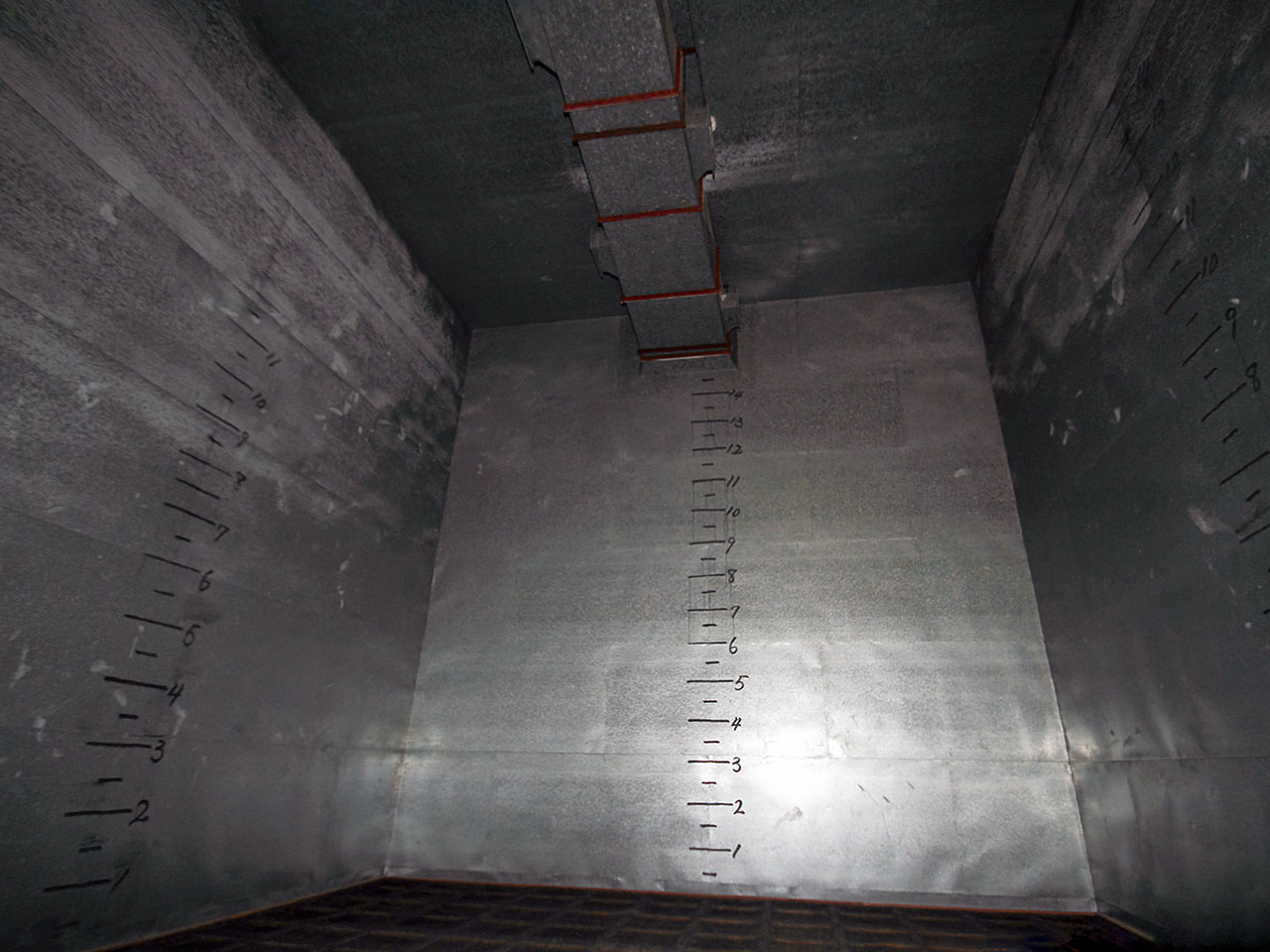
小部屋式の乾繭機のほかに、大部屋の乾繭室の2室ある。
目測だけど間口6m、奥行8m、高さ5mくらいはありそう。この巨大な空間が純白の繭でいっぱいになった時代があったのだ。
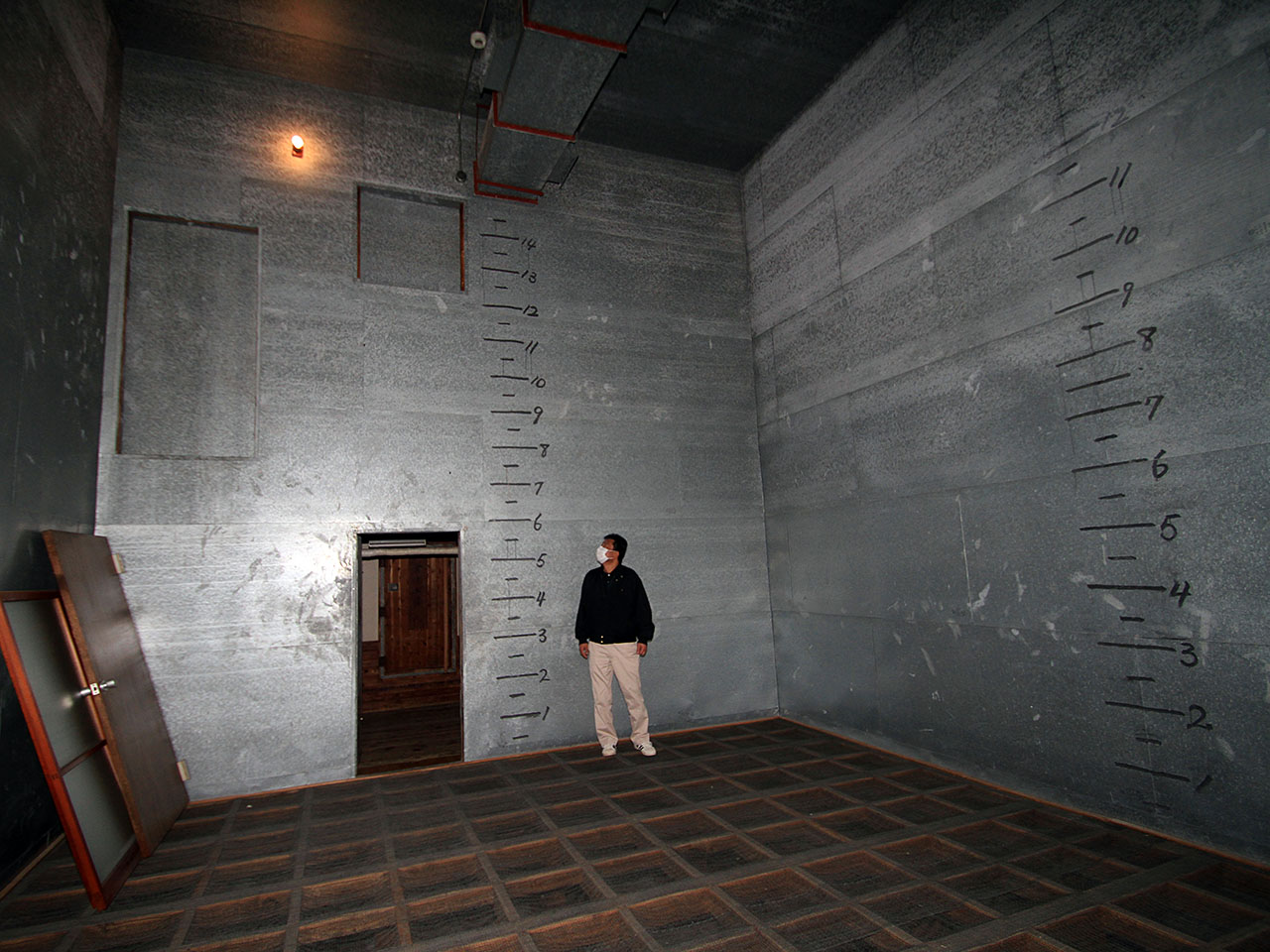
こちらにも2階の投入口がある。
このような乾燥室型の乾繭機では、その蚕期の最後の繭を乾燥後、そのまま貯繭室として利用できるという。
ちなみに、徳島県山川町や群馬県群馬町にあった乾繭工場は大和式の多段バンド型の高温熱風乾燥機だった。大和式ではベルトコンベアで繭が流れるので乾燥が終わった繭が少しずつ吐き出されてくる。それを再び繭袋に詰めて、トタン板張りの貯繭室に移さなければならなかった。
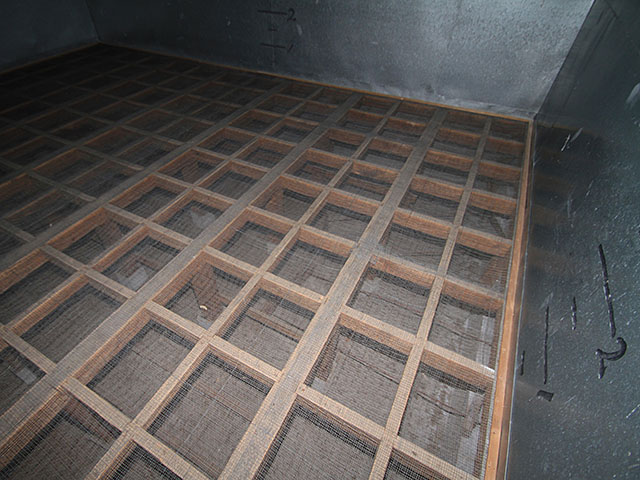
乾繭工場では高温乾燥をした藤村製糸だったが、本社工場は低温乾燥だった。低温乾燥によって繰糸時に繭糸のほぐれがよくなり、結果として生糸の品質が良くなるからだ。
藤村製糸の生糸が高品質だった理由のひとつは、この乾燥機にあったのだろう。
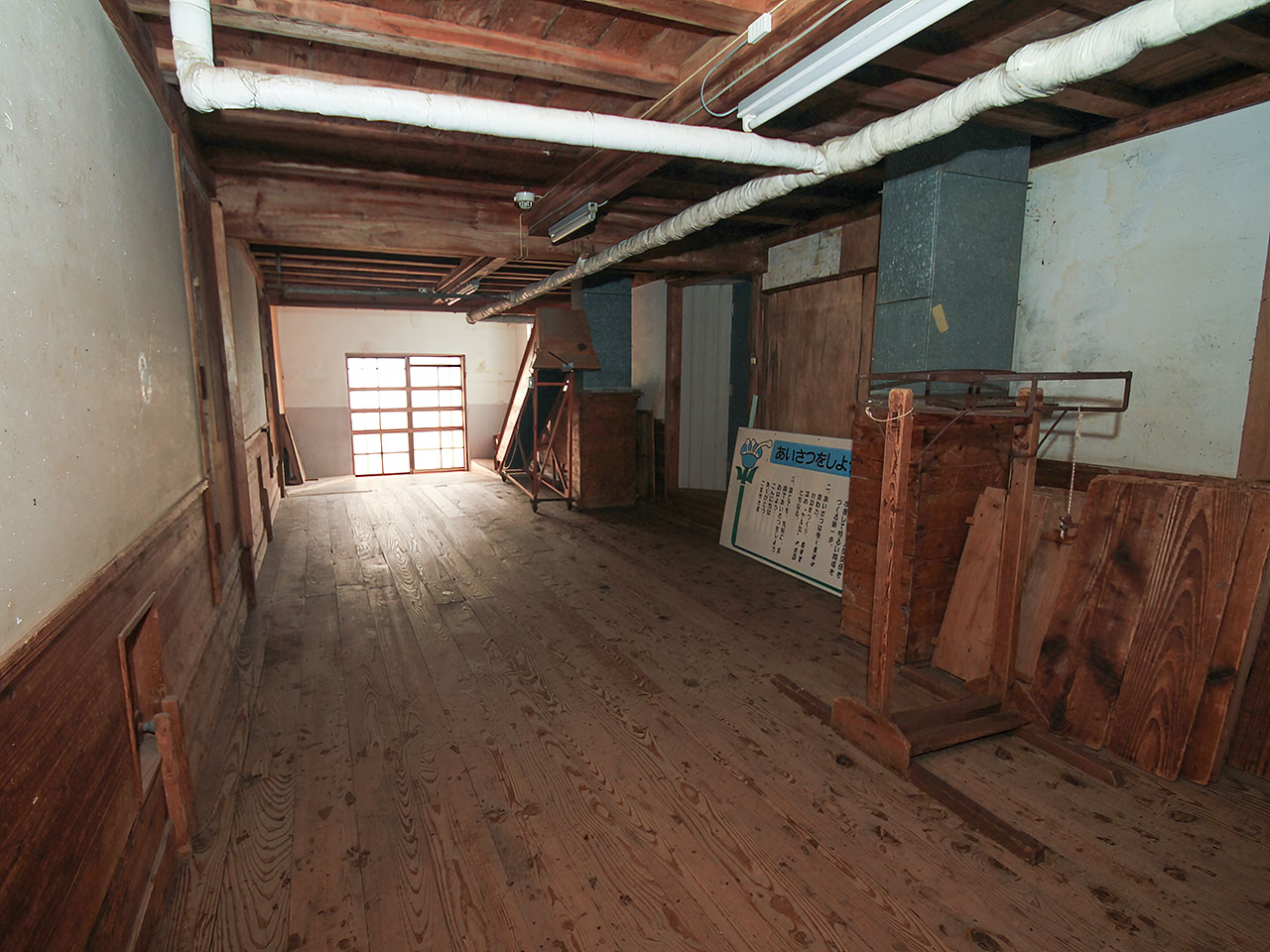
乾燥が終わった繭は写真左に写っている台秤みたいな治具を使って繭袋に詰めてから、台車に乗せて繭蔵や選繭場に運ばれる。
繭袋1袋には17kgの乾繭が入ったという。
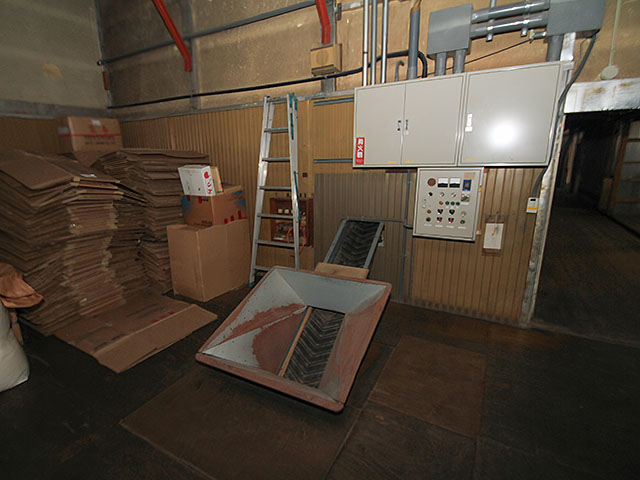
乾繭された繭が次に行くのが選繭場。
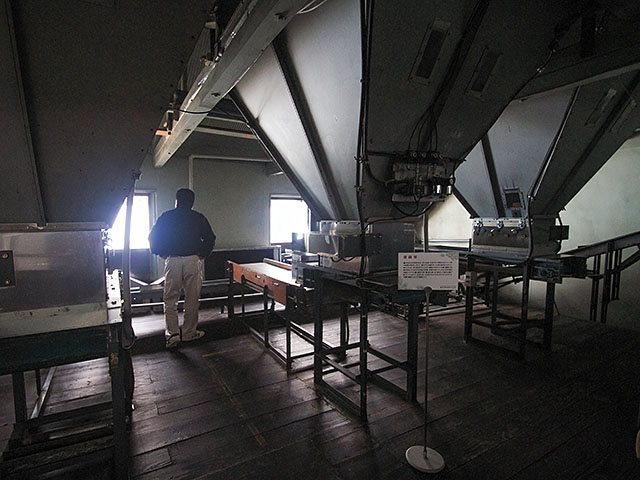
ホッパーに入れられた繭は一定量がコンベアに載せられる。
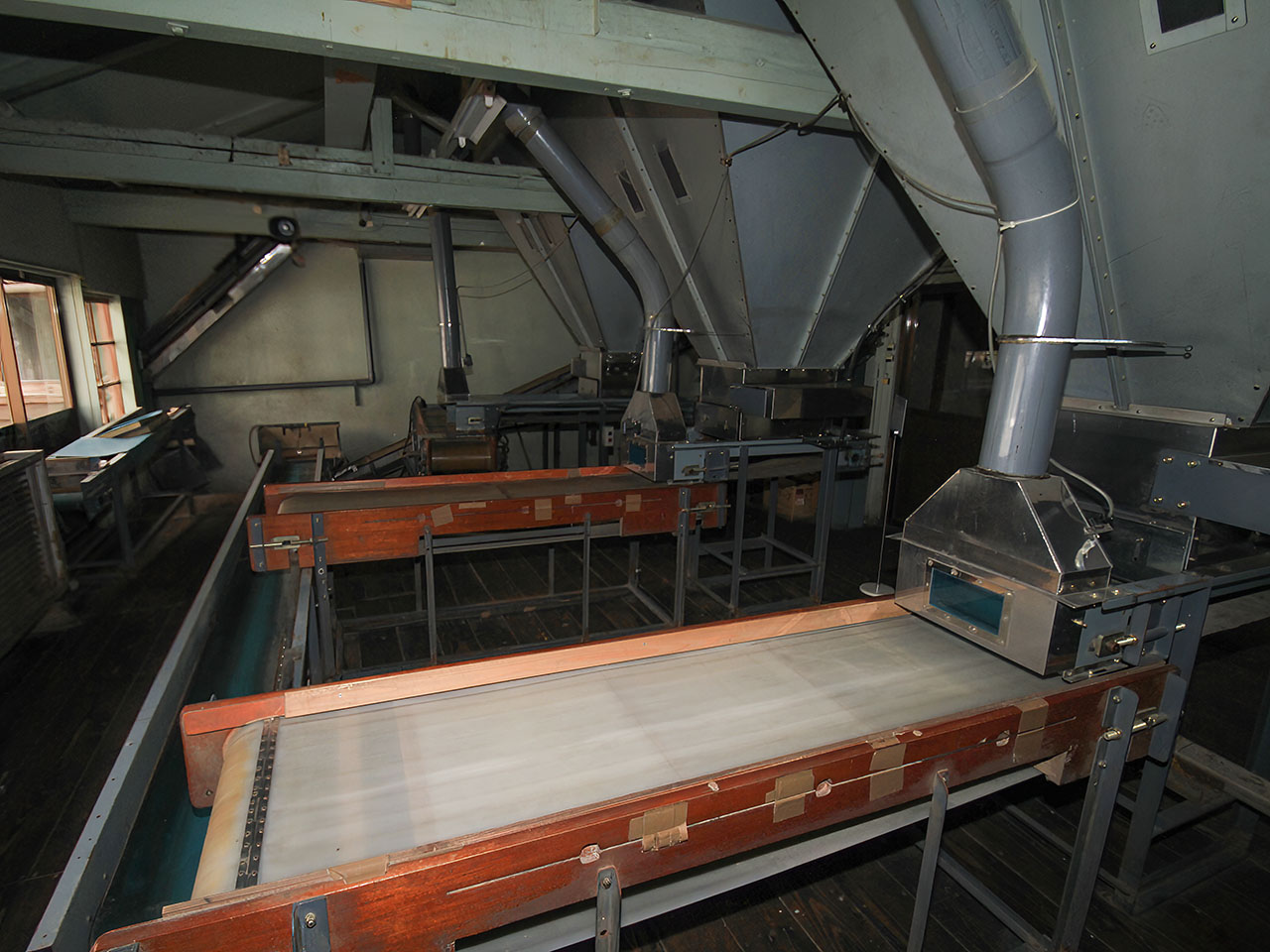
コンベアはライトテーブルになっていて、ここで不良品の繭、すなわち「選除繭」をはねるのだ。
ラインは3つあり、1つのラインに1人の検査人がいて、ほかに検査人の補助をする人が働いていたという。
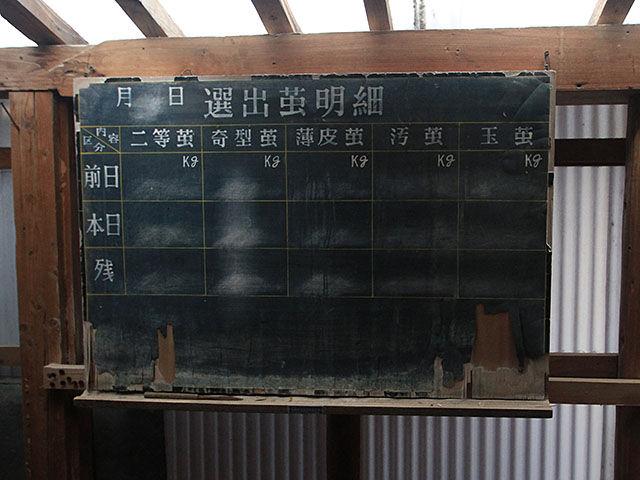
日ごとの選除繭の集計。「茧」は「繭」の異体字だ。
3行目に「残」ってあるということは、何らかの形で選除繭が消費されていたということだろう。
製糸工場内で選除繭が使われることは考えにくいから、玉糸製糸や紬工場の仲買人が買いに来ることでもあったのか。
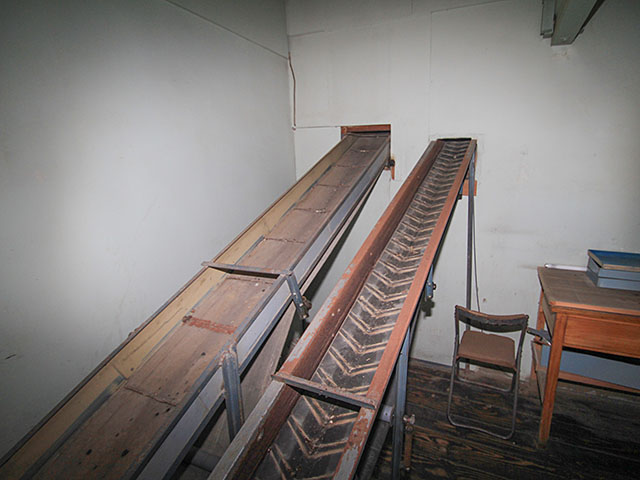
続いて、繭は煮繭機へ送られる。
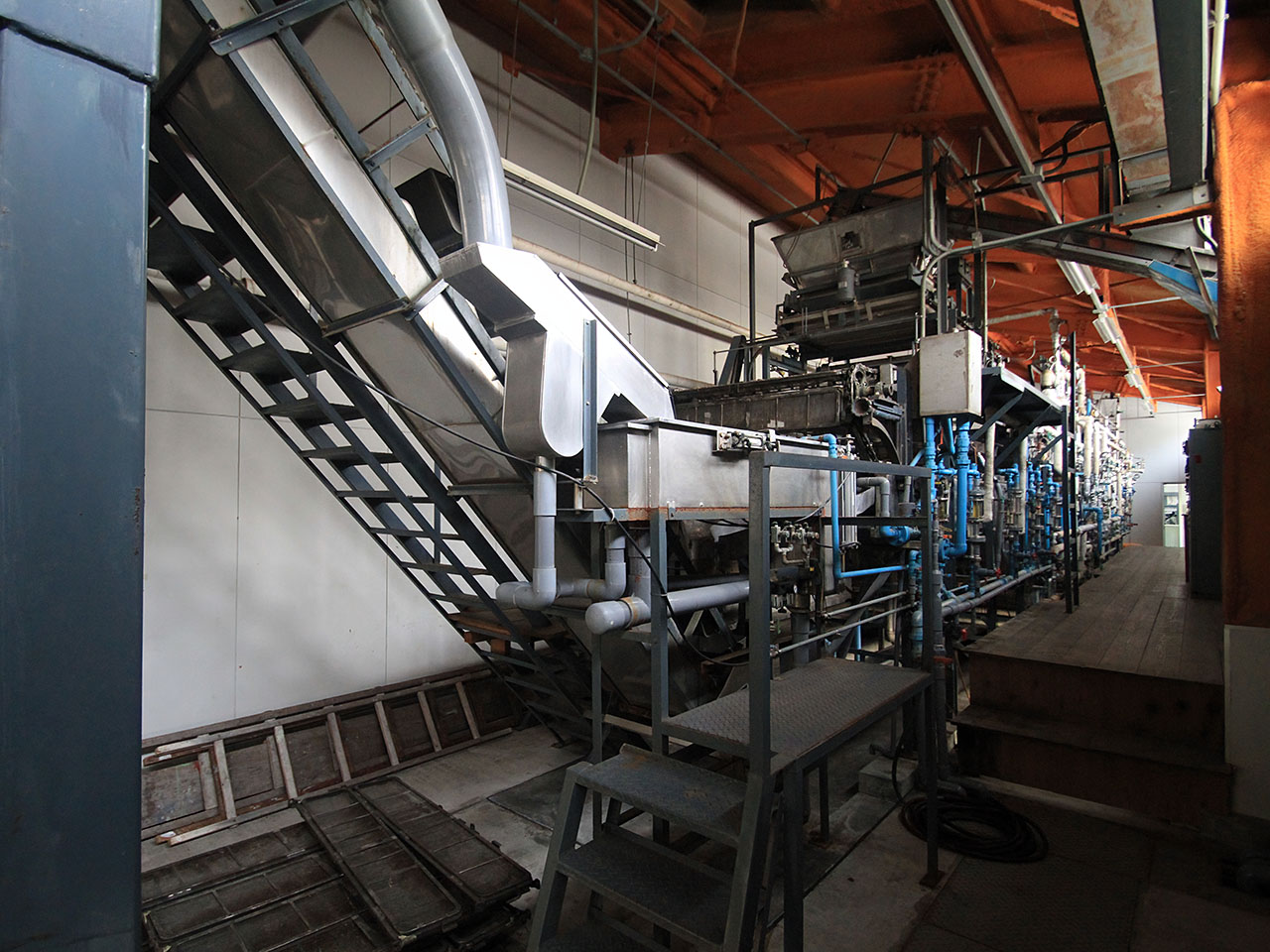
こちらはたぶん、加圧式V型煮繭機。
繭はバスケットに入り、移動しながら熱湯を潜っていく。その過程で、繭糸を固めている糊成分であるセリシンを溶出させ、また、繭の内側に湯を浸透させるのだ。
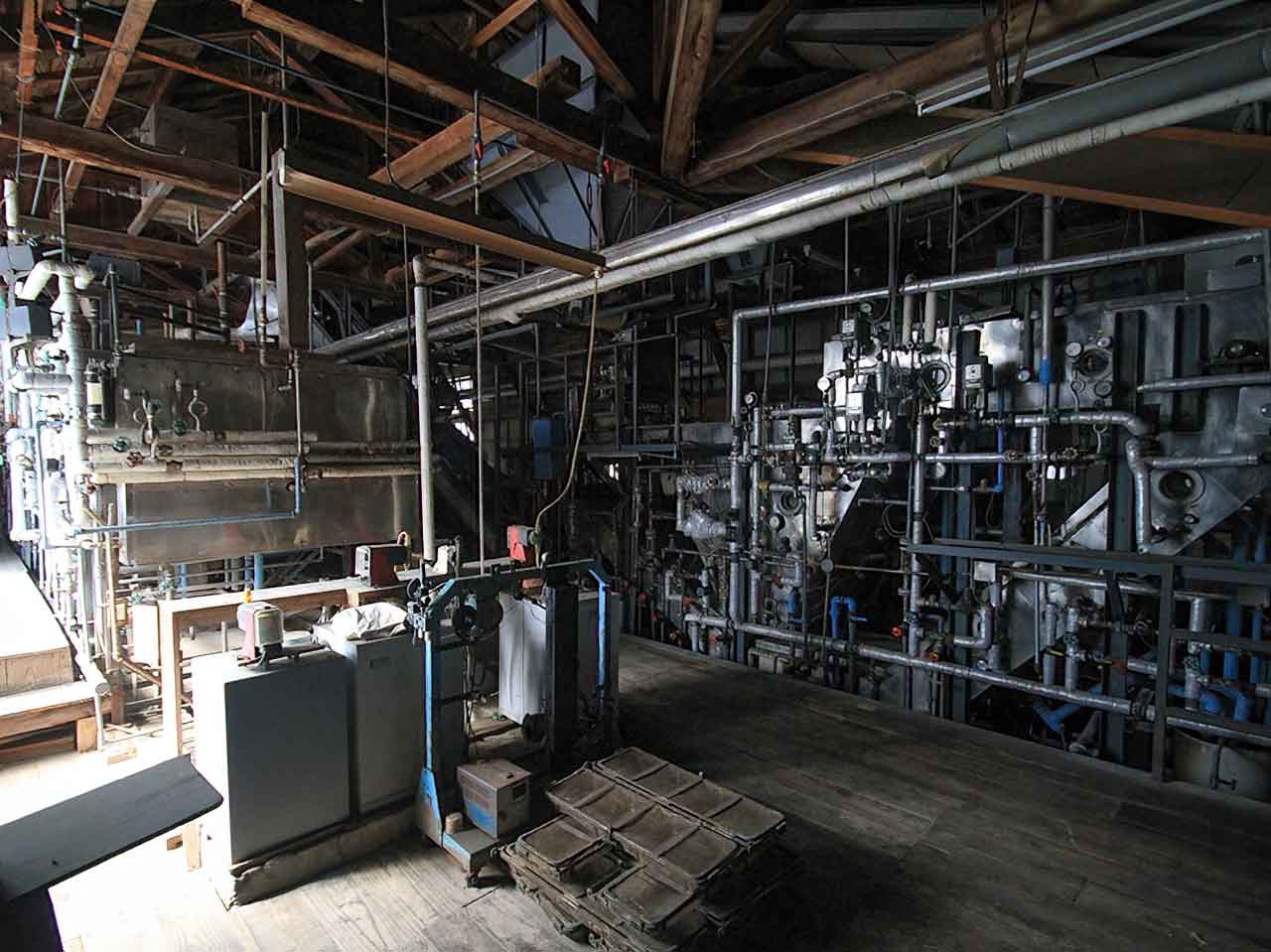
煮繭機は2台あるようだ。
写真奥側に見えるのはGHI型煮繭機というもの。

壁にGHI型煮繭機の設定のフロー図があった。全体で16分5秒でバスケットが1巡するようだ。
数字は温度ではないかな。見方はよくわからないけれどとにかく写真を撮って置こう。いつか貴重なものになるだろうから。

こちらも煮繭機の何らかの設定表。
先ほどのフロー図で1週が16分5秒なので、こちらの表によればダイアルを48にセットしたということだ。チャートを見る限り、16分は最も速いスピードということになる。
低温乾燥なので煮繭時間が短くてよいということなのだろうか・・・。
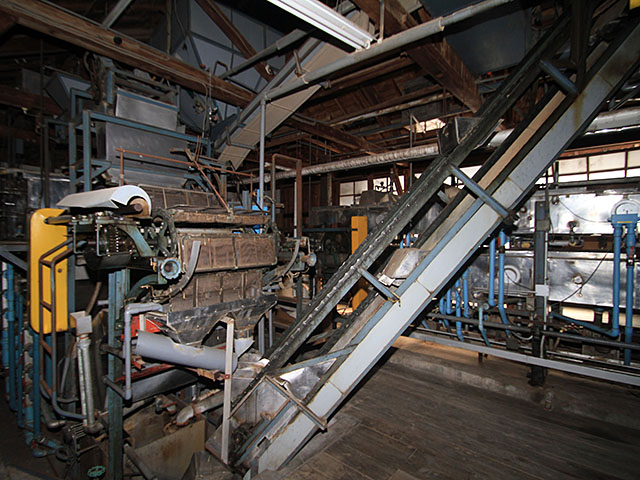
煮繭機から出てきた繭は、お湯ごとバケットに載せられ次の工程へ進む。
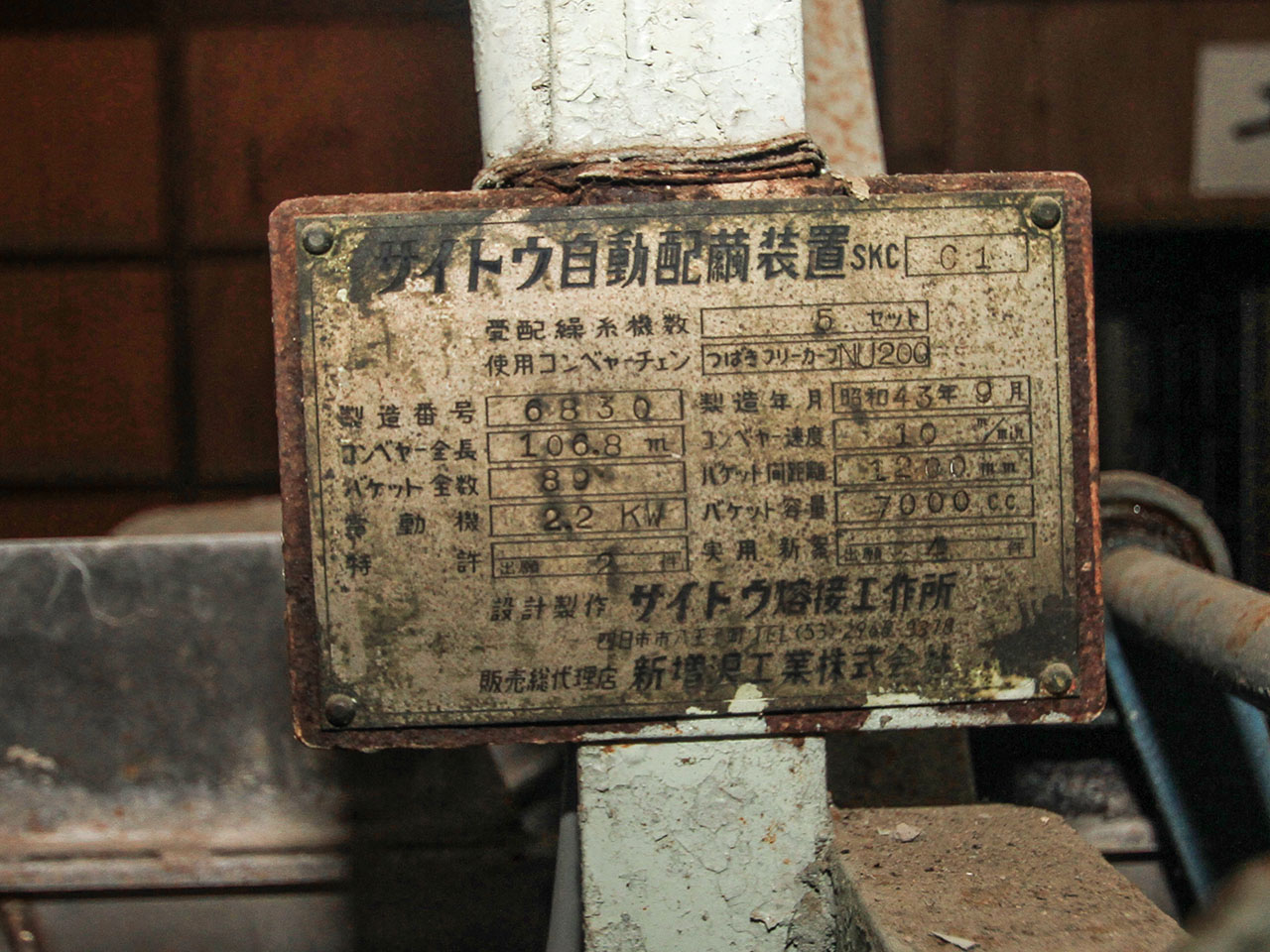
このバケットコンベアのコーションプレート。
「サイトウ自動配繭装置」とある。メーカーの「サイトウ溶接工作所」は、株式会社サイトウ工研という名前になって現存している。販売代理店の「新増沢工業株式会社」は長野県の会社でいまでも製糸機械を製造販売している。
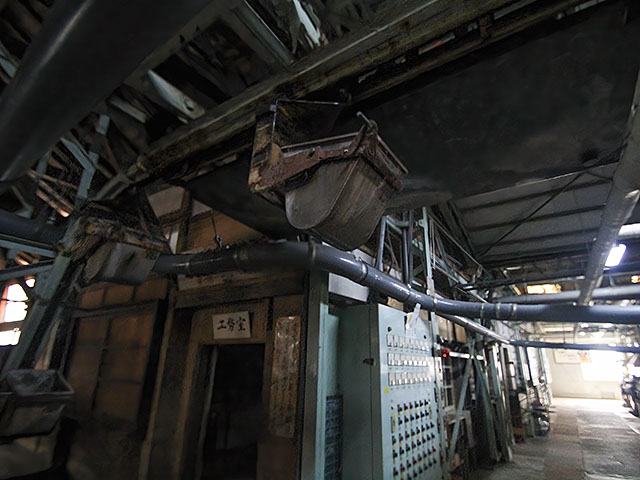
バケットは繰糸場へ。
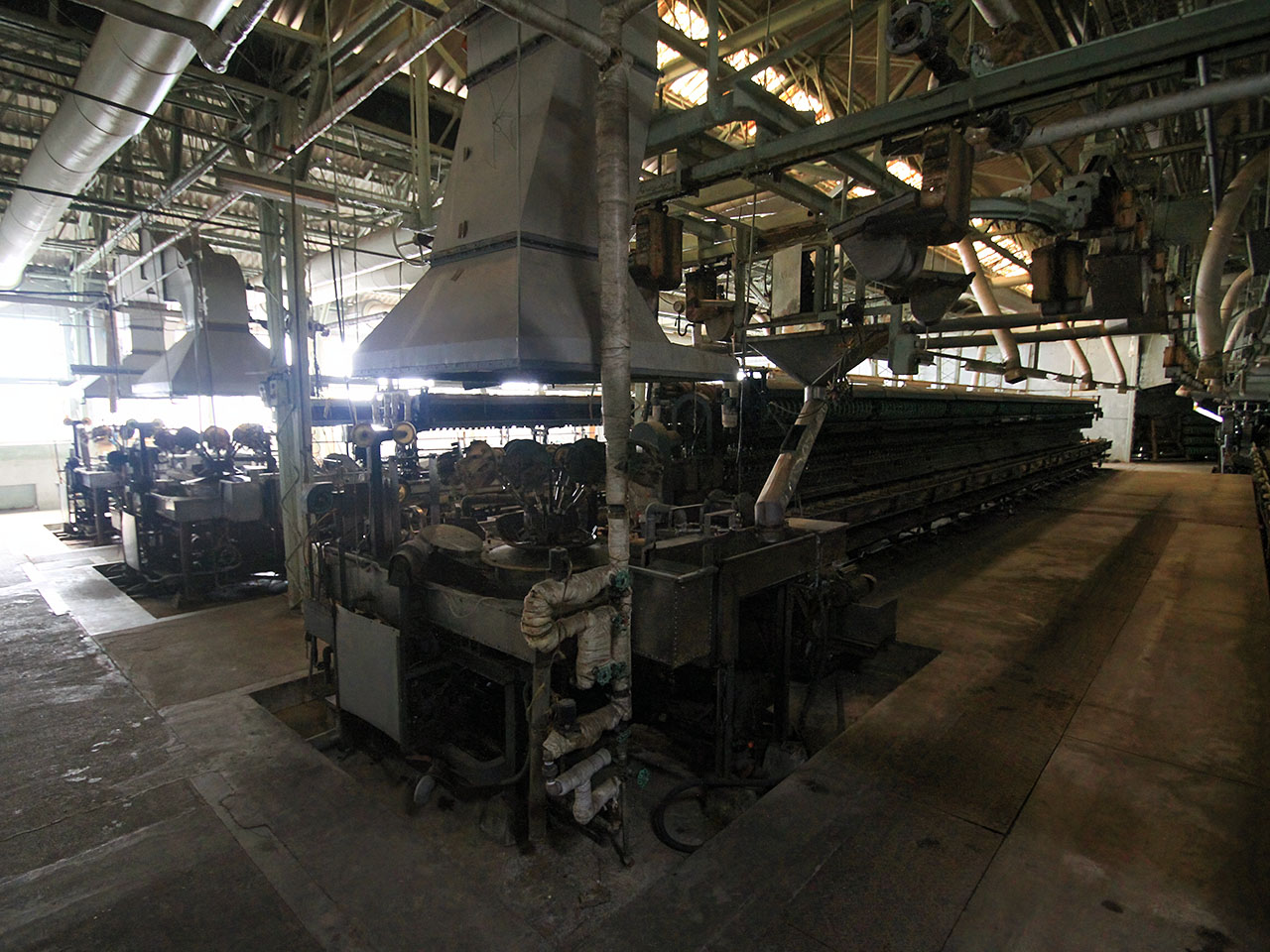
製糸工場のいちばん製糸工場らしい場所、繰糸場。
全部で5列の自動繰糸機が並んでいる。
繭はお湯ごと中央右寄りに見えるホッパーに投入され、索緒機という機械に投入される。
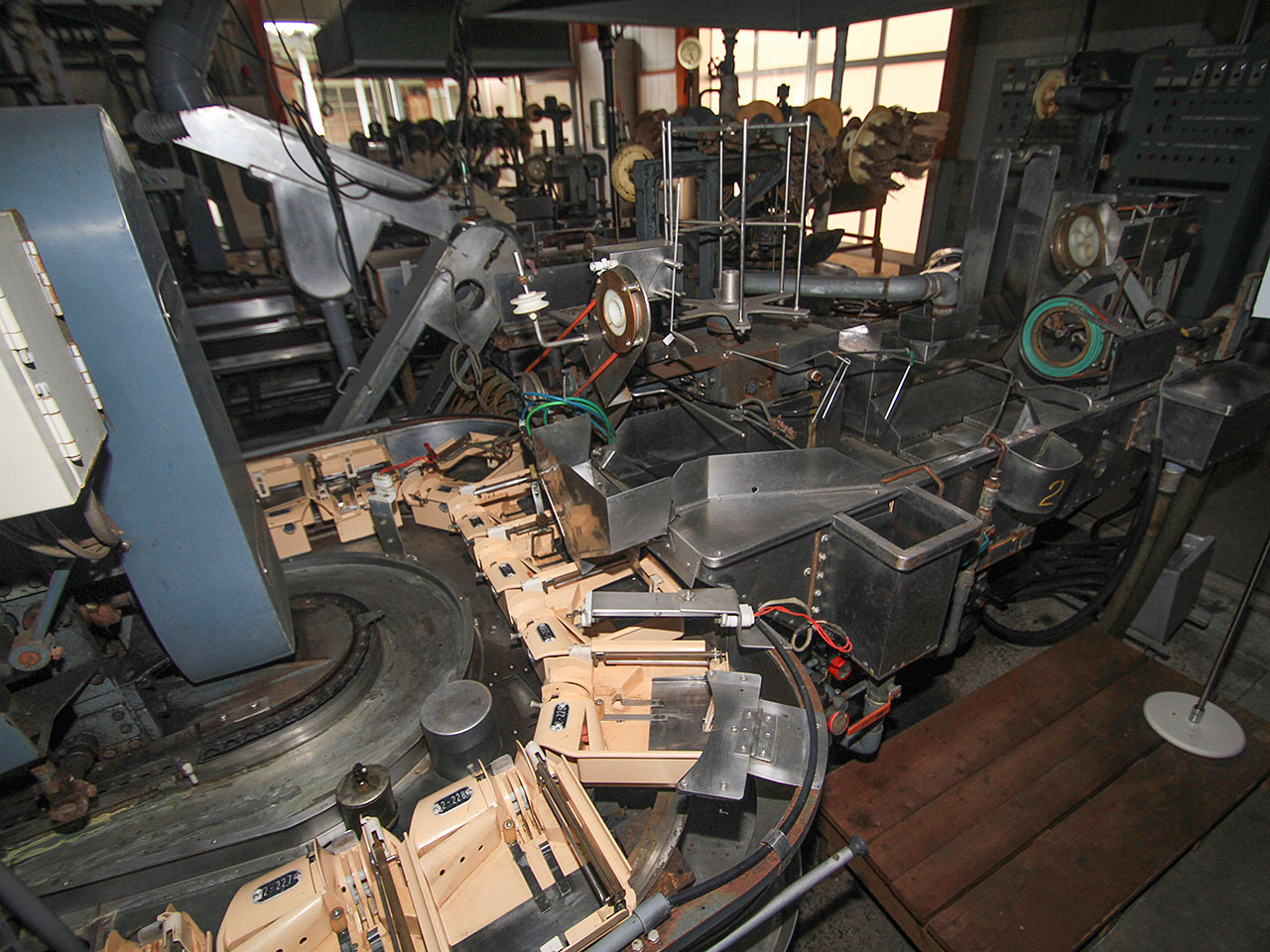
索緒機で糸口が出された繭は、ベージュ色の給繭器に載せられ、繰糸機へ。
索緒機については碓氷製糸で動作中の様子を載せているが、キビソを巻き取る枠の造りが違っている。キビソを造る仕組みは工場ごとに違うのだろうか。
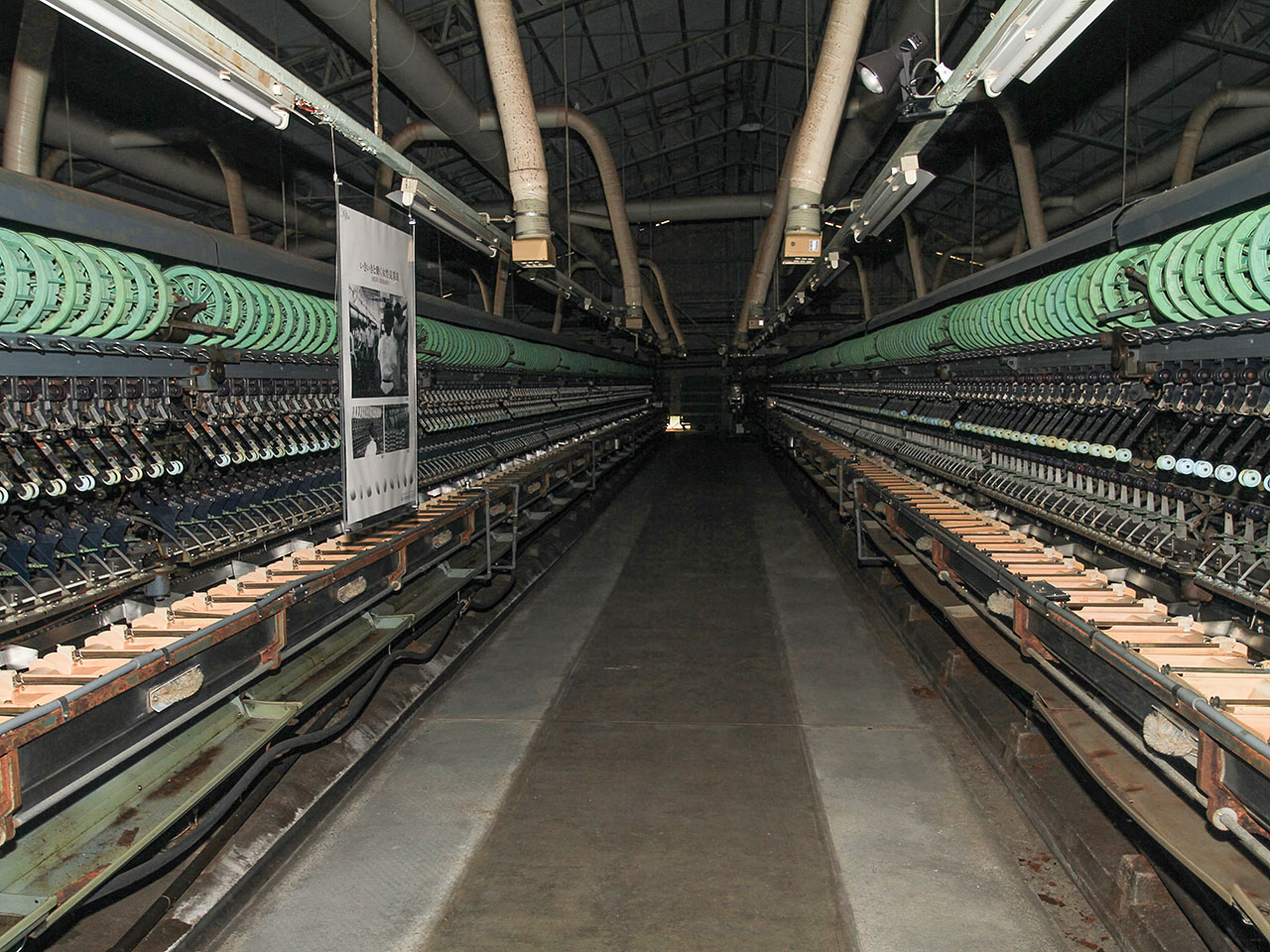
繰糸機はニッサンのHR-3。
最後に導入されたラインは平成6年(1994)で、これが日本国内で最後に購入された自動繰糸機だとされている。
いまは電気も消え、機械は静かに眠りについている。
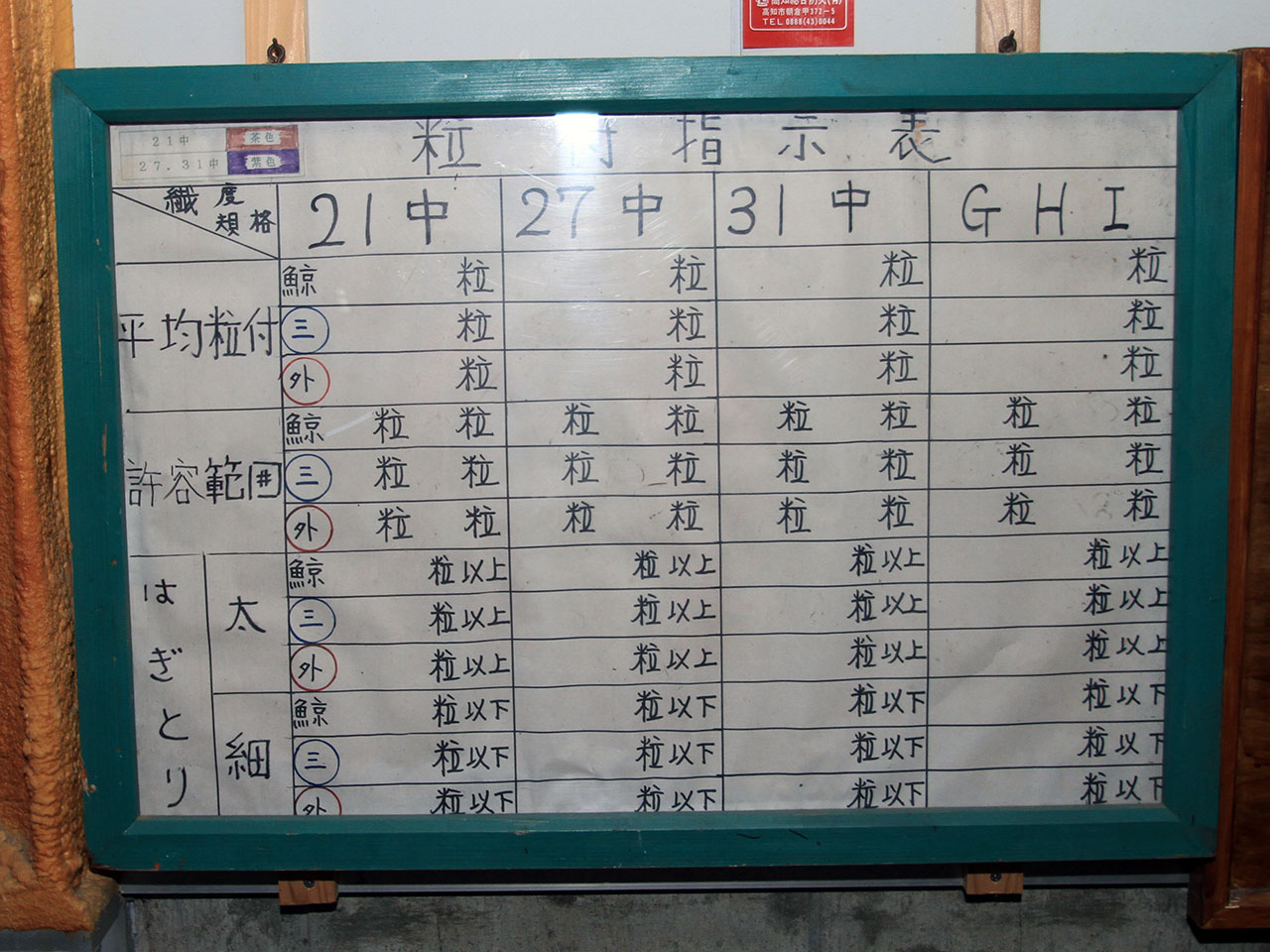
繰糸場にあった粒数指示表。
朝イチで繰糸機を始動するときの粒数の指定かな。
「クジラ」、「三」、「外」とあるのは、生糸製品のグレードだと思われる。藤村製糸のチョップ(商標)では鯨の絵のモノが最上級のグレードだったと聞いている。創業者の藤村米太郎が捕鯨家だったことにちなむデザインだ。
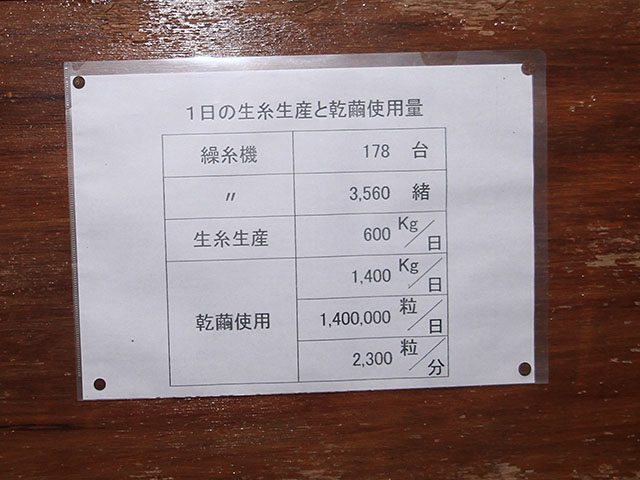
こちらは見学者用に貼られた繭の使用量。おそらく全盛期の生産高ではないかと思う。全盛期には200人以上の従業員がいたという。
藤村製糸では1日に600kgの生糸を生産できた。生繭にして3.4トン程度になる。年間250日操業したとすると、年に850トンの繭が必要になる。現在の日本国内で生産されるすべての繭よりも多い繭が必要な工場だった。
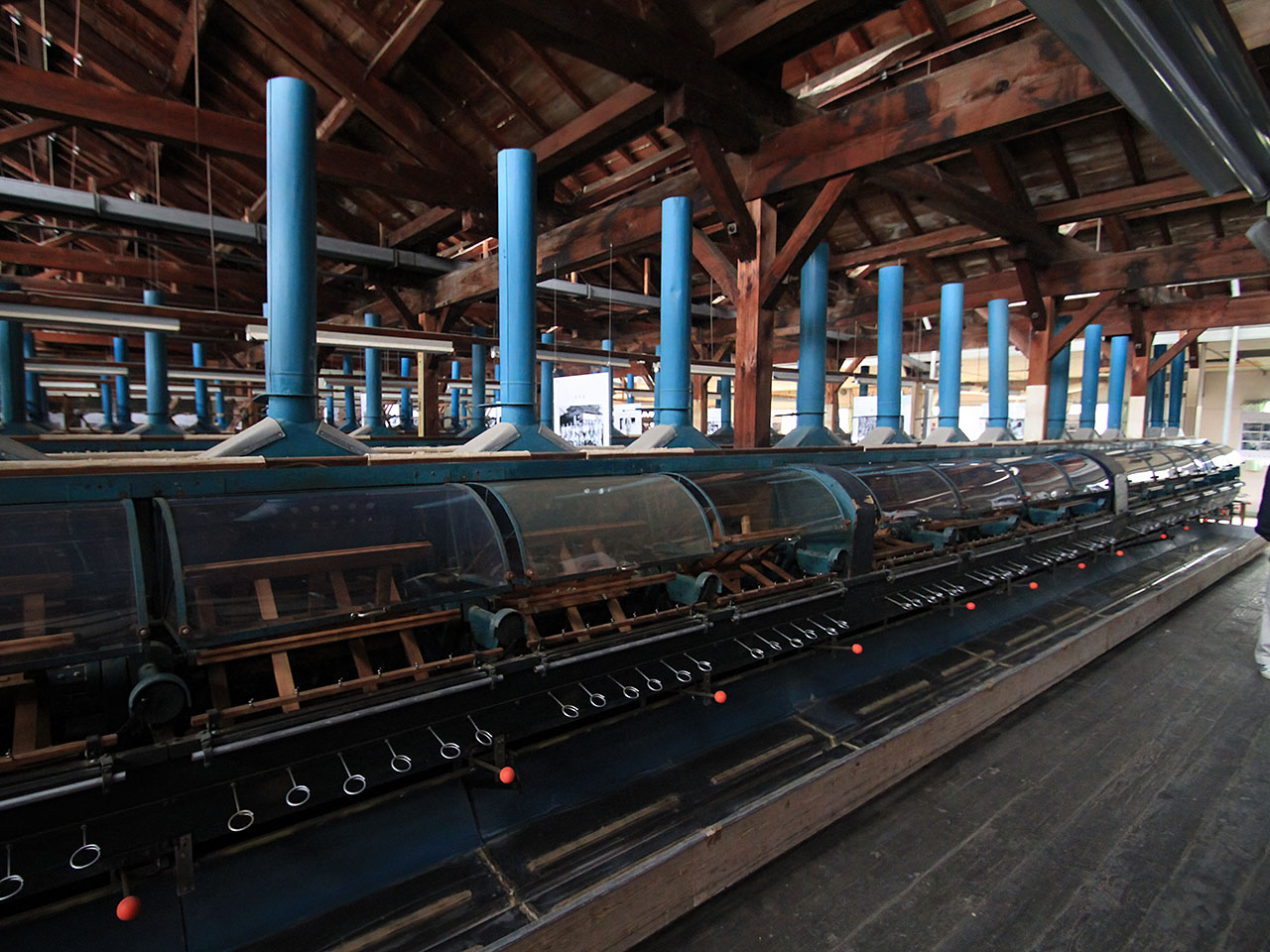
続いて再繰場へ。
繰糸機で小枠に巻かれた生糸を大枠に巻き直す工程の場所だ。
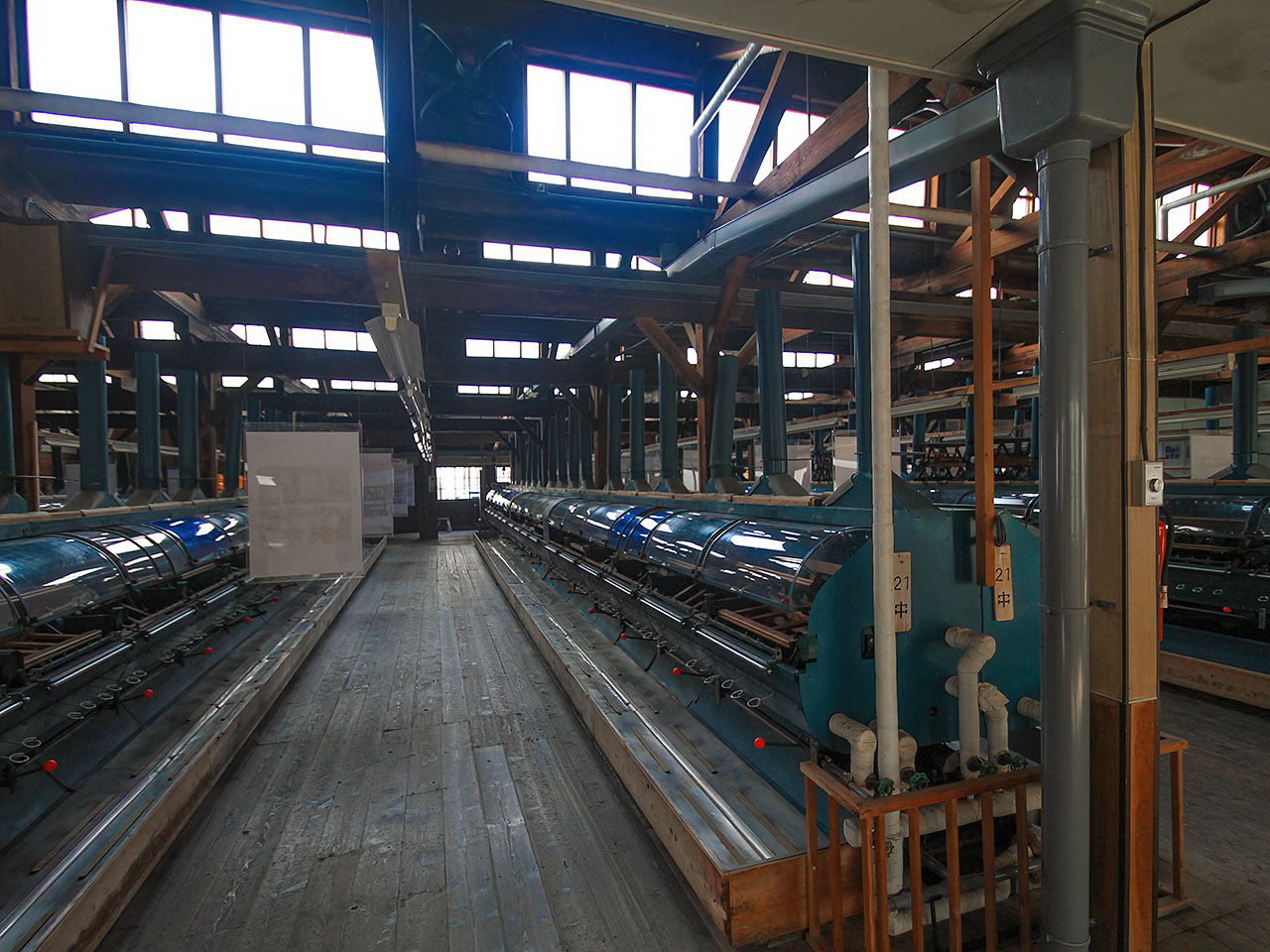
ここの特徴は社屋が木造トラス構造のノコギリ屋根になっているということ。
昭和に育った人たちにとって、工場といえばノコギリ屋根というイメージだが、実際には珍しくなった。製糸工場うんぬんという以前に、ノコギリ屋根の工場があるだけで目が釘付けになってしまう。
昔は照明が不安定で自然光に頼っていたが、現代では逆に天候によって光量が変わるこの仕組みは望ましいものではないし、建築構造的にも雨仕舞いが悪そうなので、新たに建設されることはないのだろう。
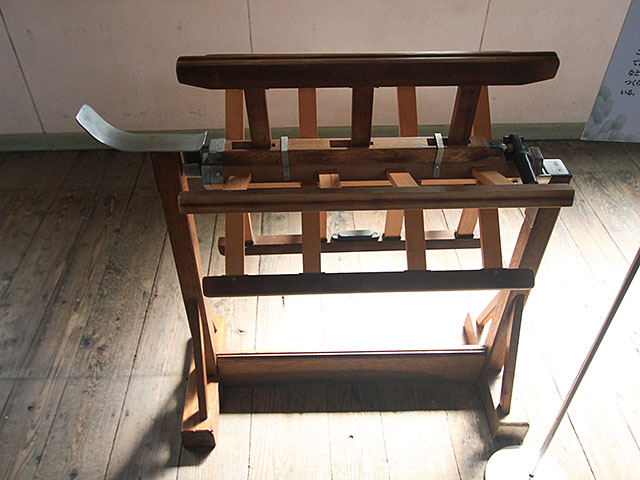
再繰場の片隅にあった大枠を仮置きする台。
隣にはあみそ糸についての説明板があったので、もしかすると見学者にあみそ掛けのデモをしたのかな。
道具としては通常に使用するものではなく、事故で糸口がわからなくなったときなどに、丹念に修復するための台ではないかと思われる。
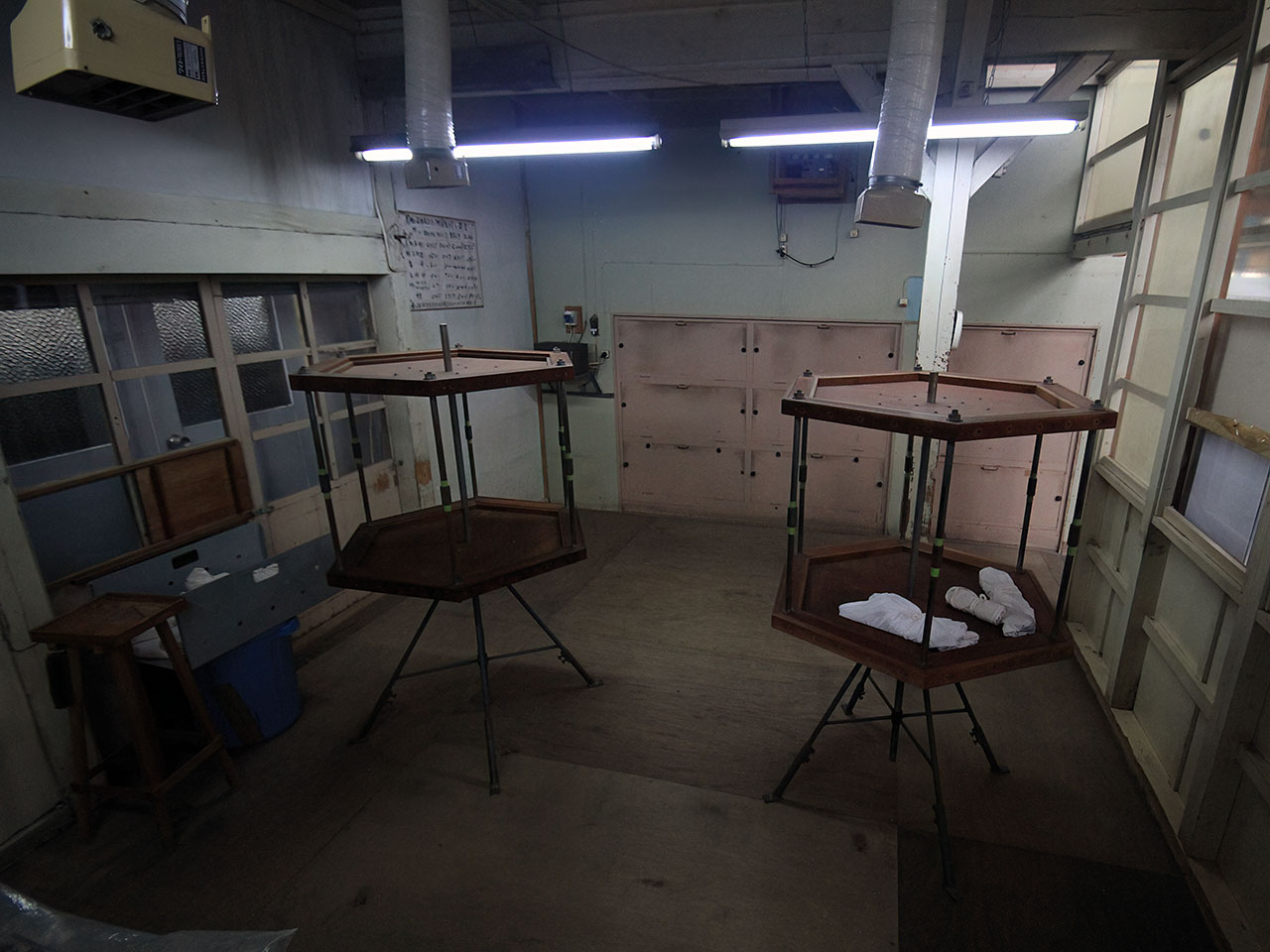
仕上室。
生糸を最終的な荷姿にして梱包するための部屋だ。
生糸の荷姿は「綛」といって1周1.5mの枠から外した帯状のものだ。綛の作り方は過去にさまざまな技巧を凝らしたものもあったが、最終的には長手造りという形式で出荷していた。
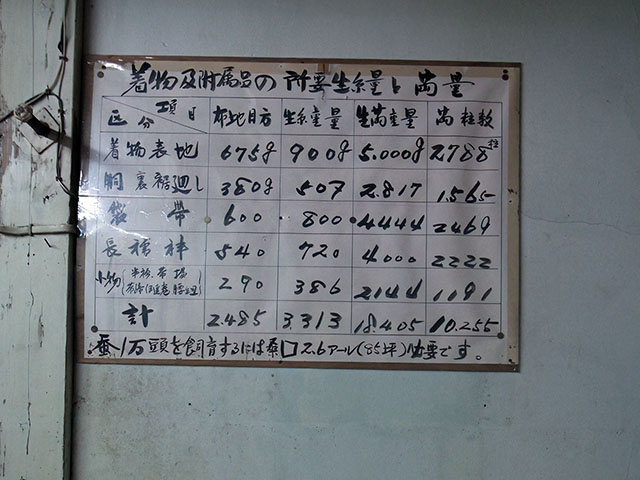
仕上室にあった製品と生糸の使用量の対応表。
これもかつての見学コース向けの資料だったのだろう。
たまに博物館などで同様のものを見かけるけれど、胴裏、帯、長襦袢といった製品の糸量まで書いてあるものは珍しい。
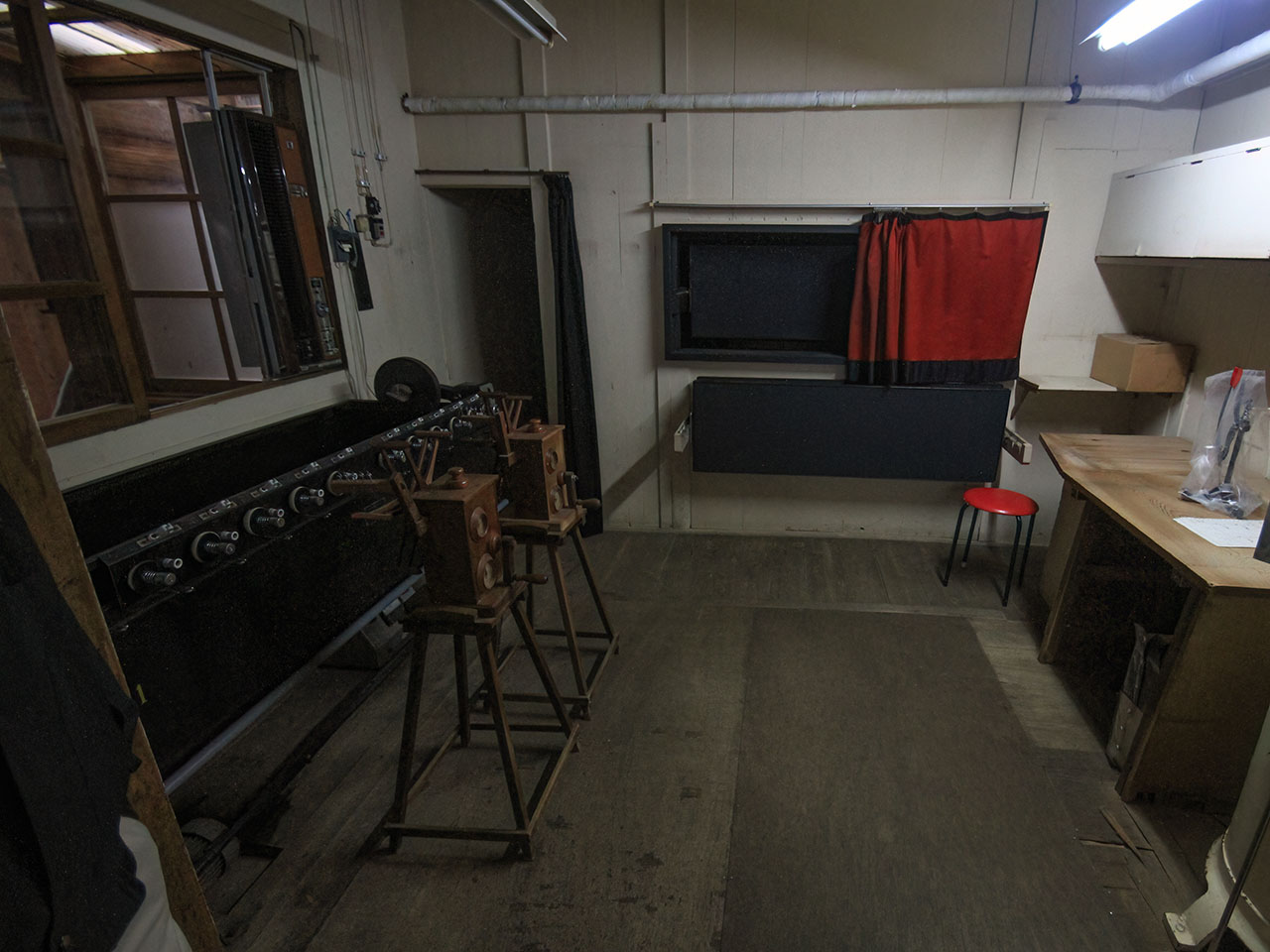
続いて、生糸の品質を検査するためのセリプレン室。
生糸の品質を決める指標はいくつかあるのだが、糸の太さのムラや、蚕が糸を吐くときにスムーズに吐けなかった箇所が糸に現れてしまっている箇所の量などが基準になる。これが少ないほど良い糸ということになり、それを調べるのが糸条斑検査や、節検査だ。
奥に見える黒い板にサンプリングした生糸を巻き付け、サンプルと比較して採点していく。
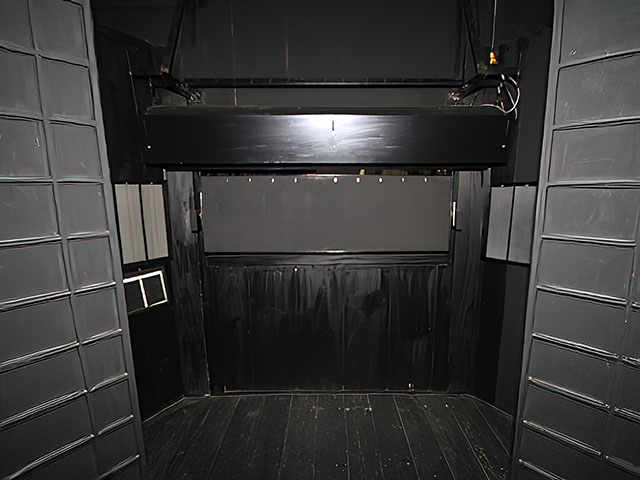
その検査を一定の基準で行えるようにした暗室がセリプレン室だ。
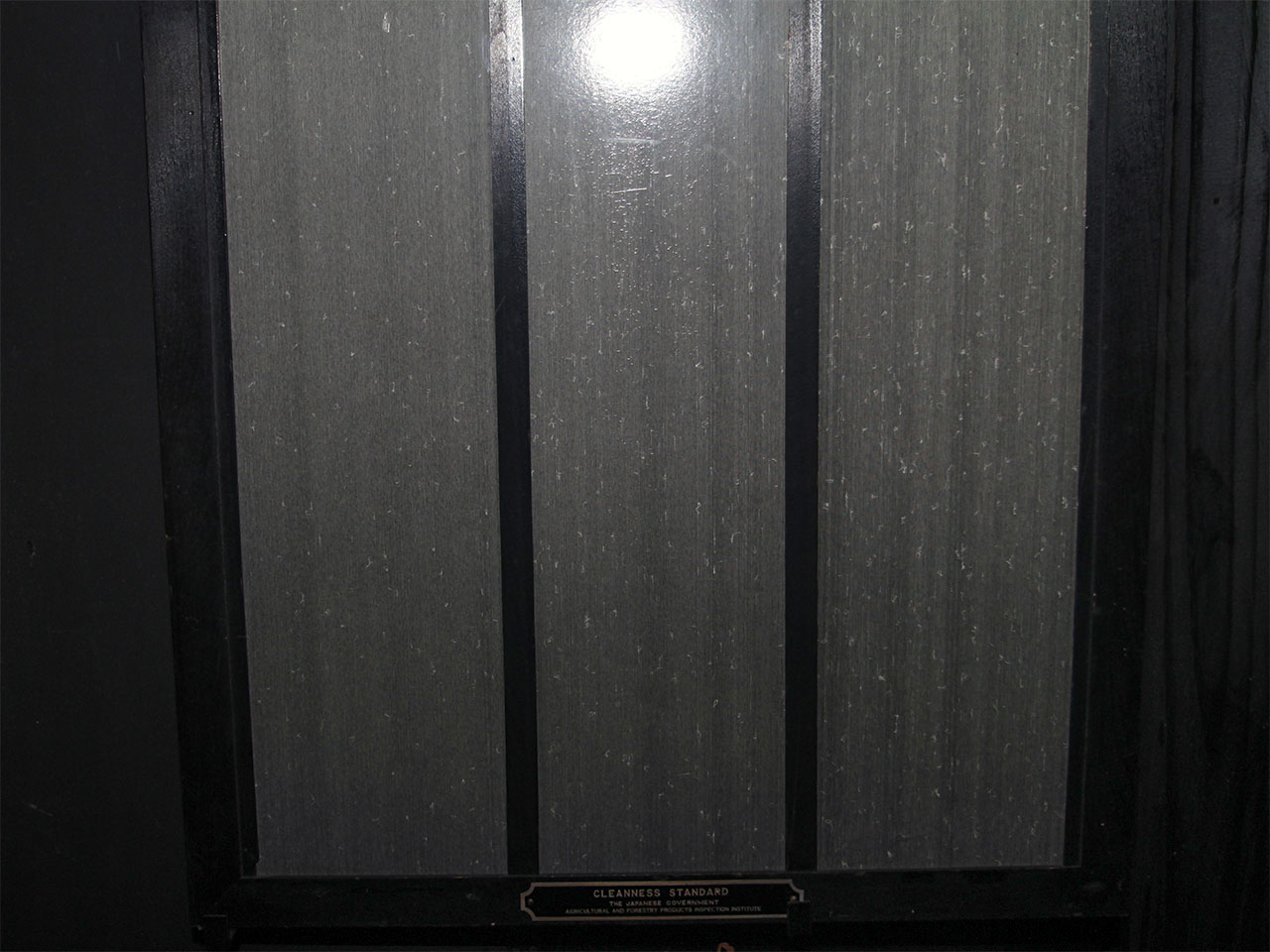
こちらが基準となる試料。白い点のように見えるものが「
検査対象の糸を巻いた板と、試料の板を人間の眼で比較して、近いものを選んでいくという方式。
現代ならAIでもできそうだけれど、人間の眼も侮れないからそれなりに正確な検査ができたろうと思う。
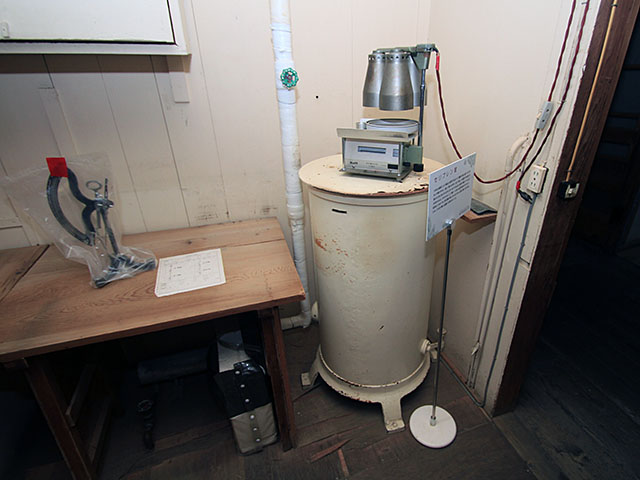
このドラム缶みたいなものは「水分検査器」。生糸の重量を量る際に、糸の水分量をゼロにするための乾燥機だ。生糸の重量は水分量ゼロのときの重さに対して、標準的な水分相当として11%の重量を加算して求める。
左側にある弓型の機械は「
サンプリングした生糸の太さが安定していることも品質の条件になっている。
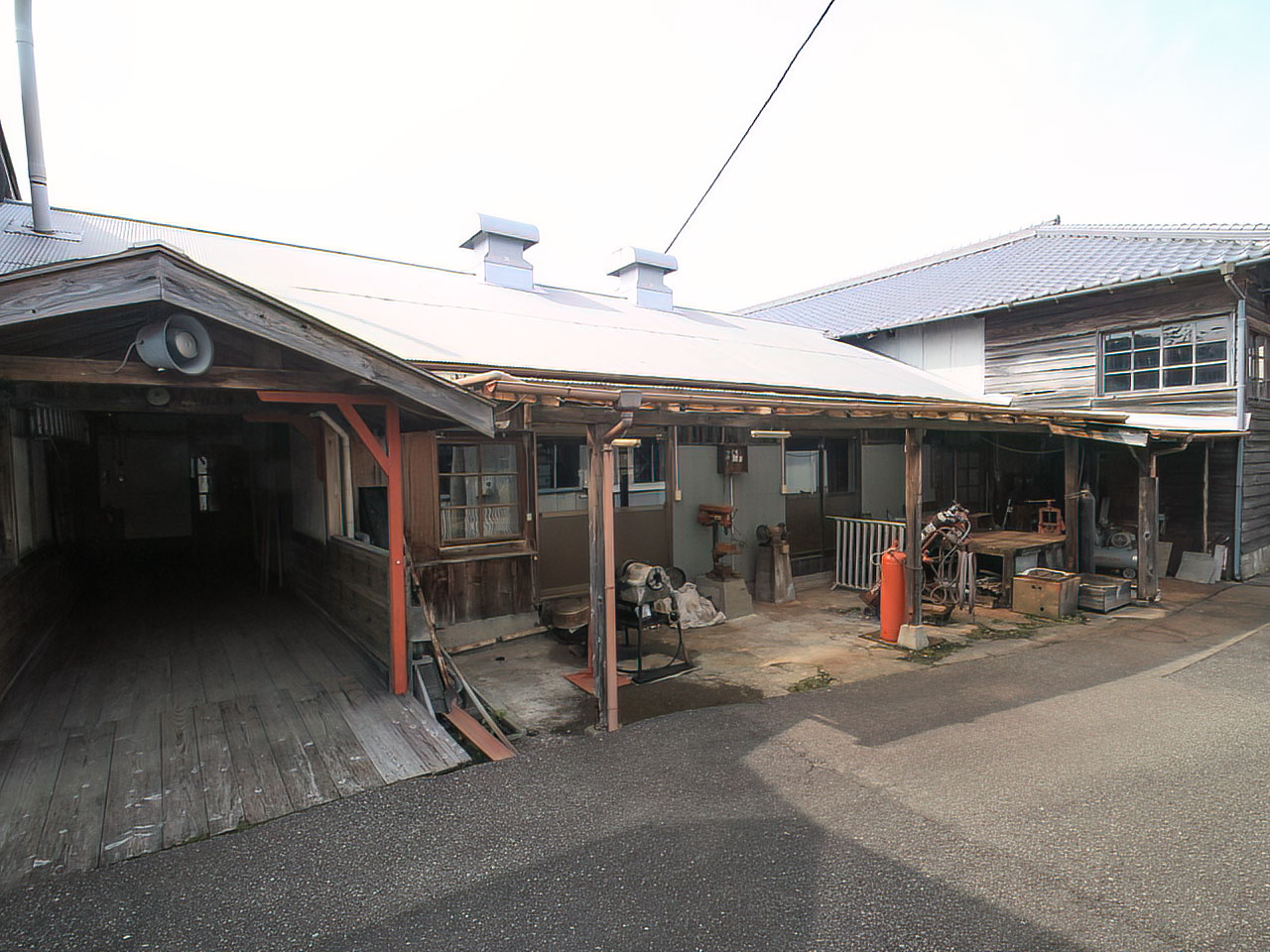
続いて副蚕場へ。
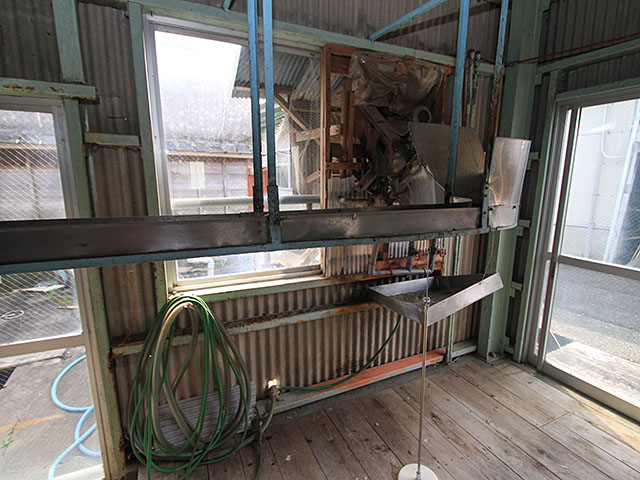
繰糸場で糸が取れなくなった繭の残りが送られてくる場所だ。ここでビスという製品が作られる。
碓氷製糸でもちらっと見学させてもらったが、ここではじっくり見ることができた。
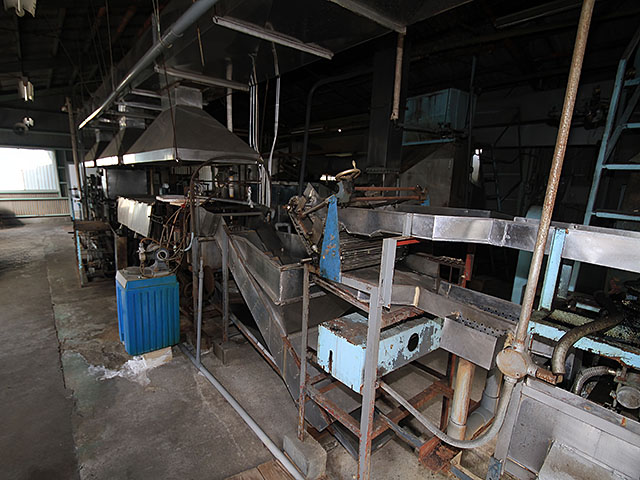
これはビス整理機と呼ばれる機械。
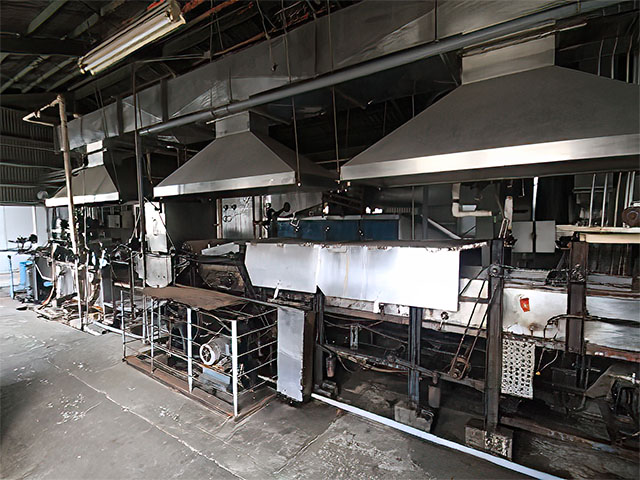
たぶんグンゼ式と呼ばれる形式のもの。
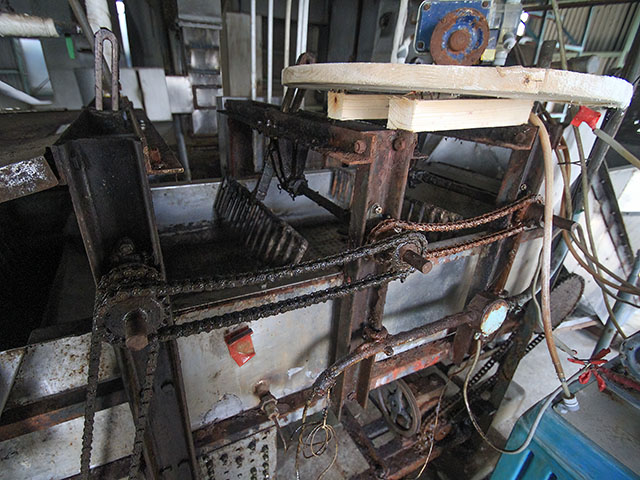
サナギの油やタンパクが分厚くこびりついていておどろおどろしい感じ。
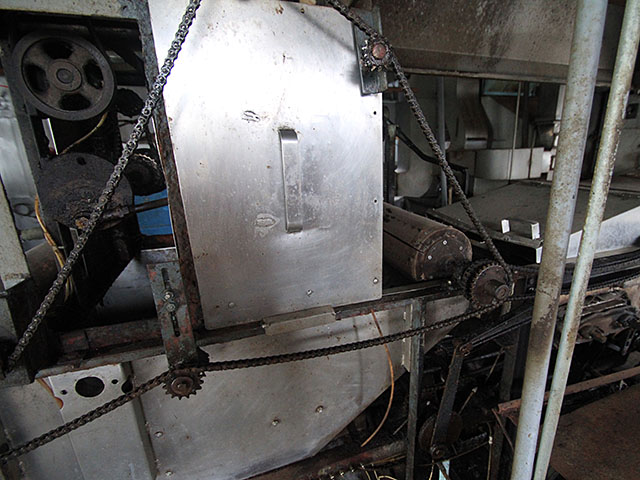
仕組みはよくわからないけれど、いくつかのローラーで残った繭層を巻き取っていくものだと思う。
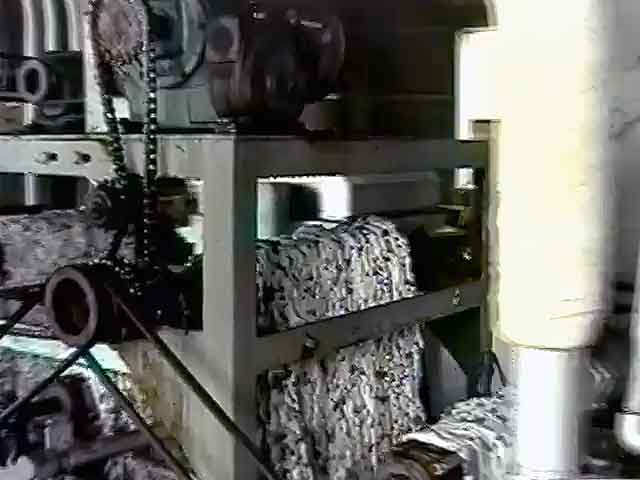
これは操業時にこの機械が動作しているときの様子。
繭とサナギが一緒に巻き上げられているのが見える。
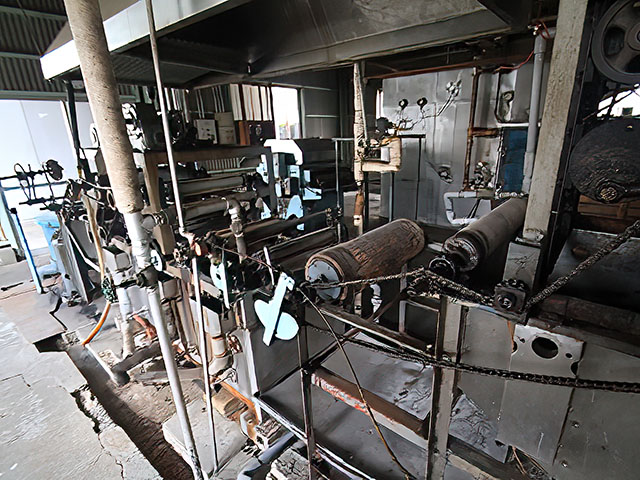
どういう動作原理なのかまったくわからないが、いつかのためにとりあえず写真をとっておこう。
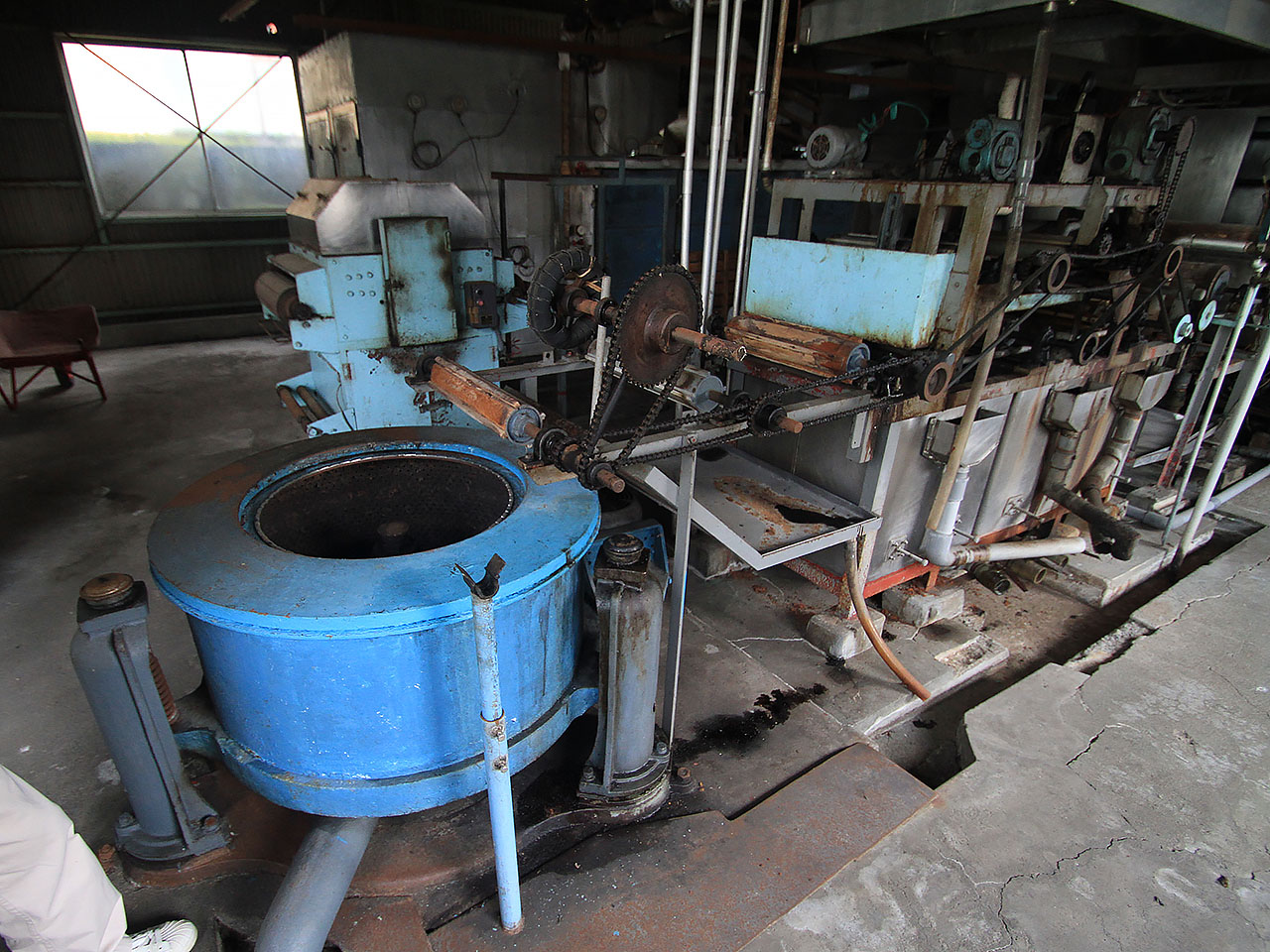
機械の出口には業務用の脱水機があった。
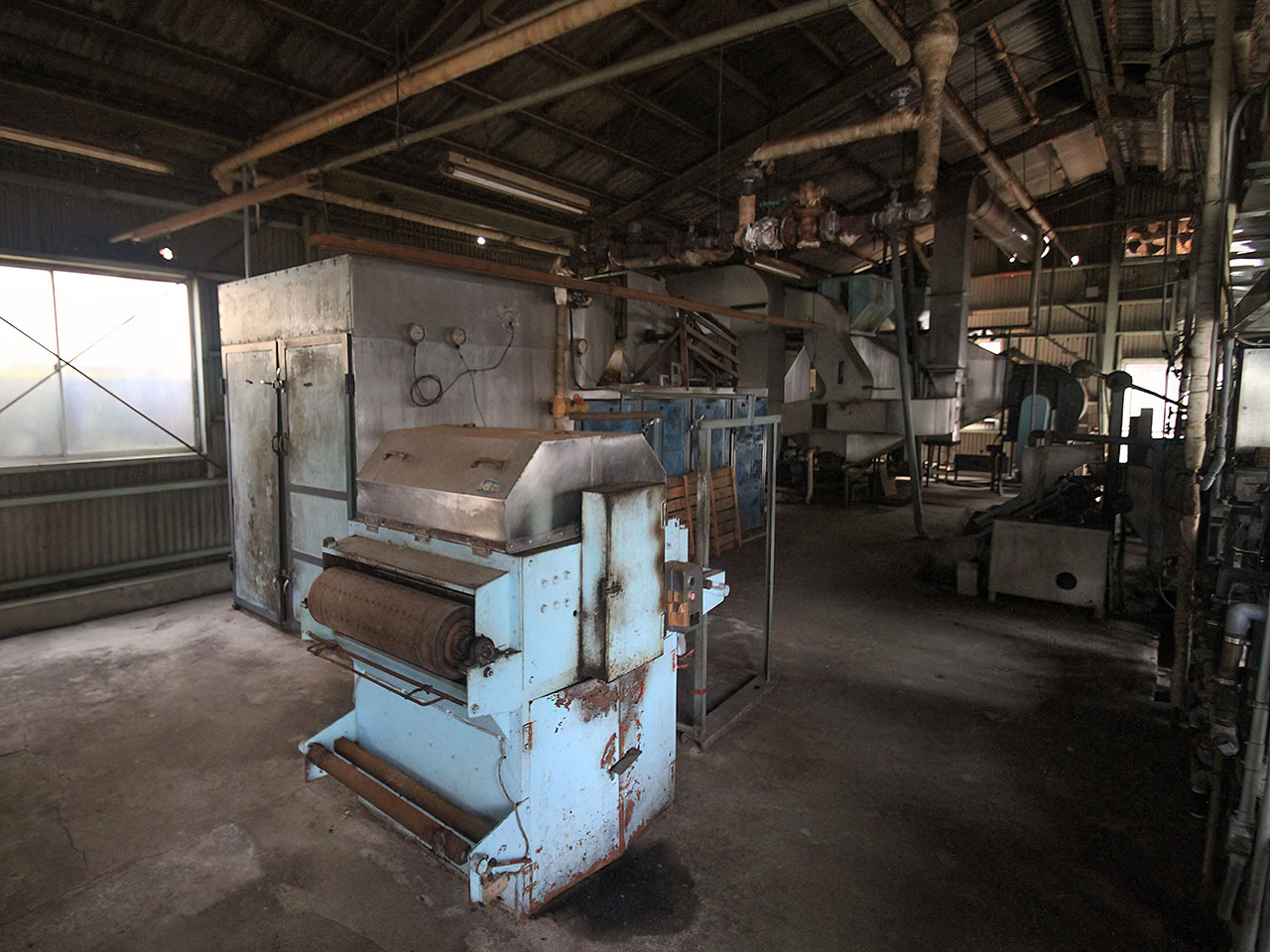
こちらはビス叩き機という機械。
サナギを除去するのか、あるいは、乾燥したビスをふんわりさせるものだろうか。
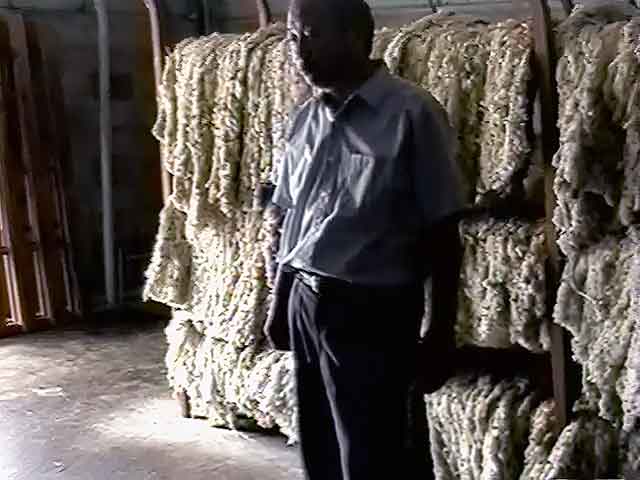
操業時のビスの仕上がり。
ビスはこのあと紡績工場に販売されて絹紡糸になる。
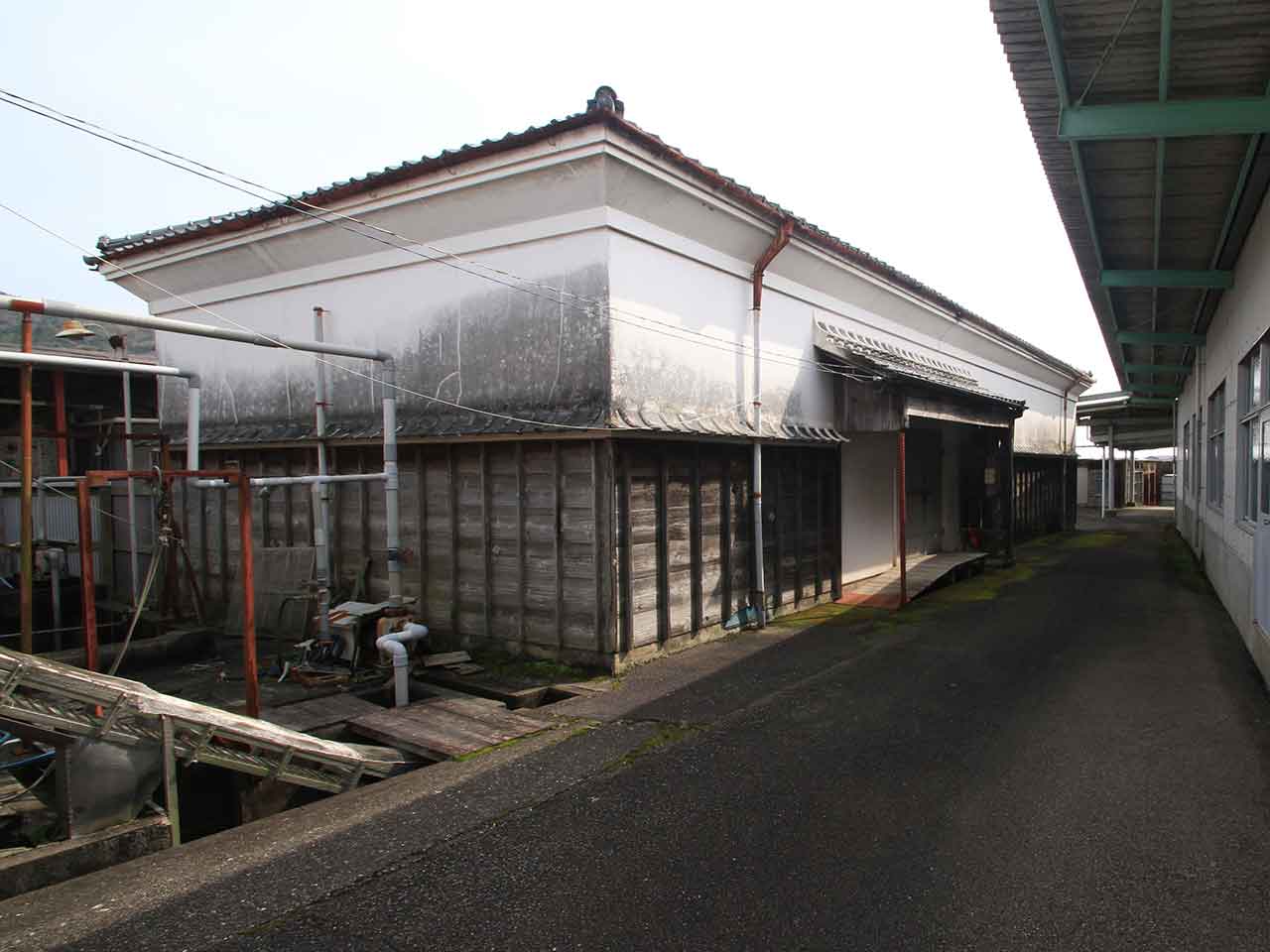
副蚕場の横にあった東繭蔵。
この工場でも初期に建てられた建物だろう。
最終的には副蚕物の保管庫だったのかもしれない。
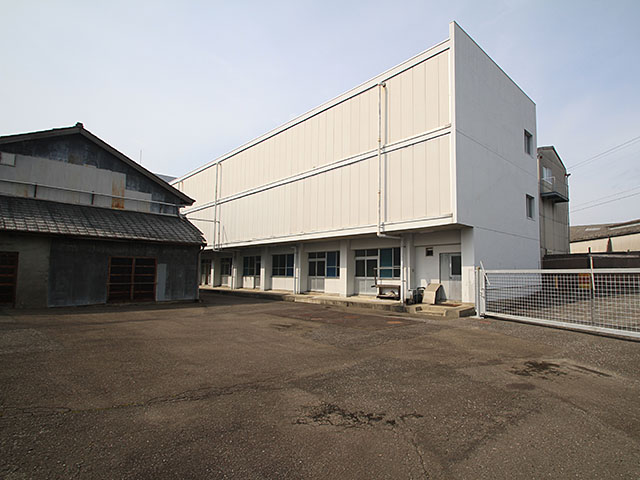
こちらは従業員食堂や寮かな。
ほかにもいくつか見せてもらった機械もあったが、どこかで紹介したものとダブるのでここまでとしたい。
とても広範囲に見学させてもらえたし、乾繭機の内部や副蚕場も丁寧に見せてもらえたのはうれしかった。
藤村製糸さま、ありがとうとざいました。
残念ながら藤村製糸本社工場は、この翌年、2013年に取り壊されてしまった。
入口横の西繭蔵は残っていて資料館が見学できるが、それ以外の部分は太陽光発電所になっている。
(2012年03月19日訪問)